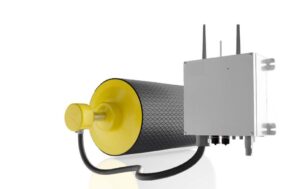
Rulmeca is proud to introduce the Rulmeca Monitoring System (RMS), a new solution for… Read more »
Rulmeca is proud to introduce the Rulmeca Monitoring System (RMS), a new solution for… Read more »
The rise of ecommerce has changed the retail landscape irrevocably over the last couple… Read more »
Headquartered in Leeds, Farnell Ltd, an Avnet Company, is a global distributor of electronic… Read more »
Ed Wainman, Aftersales Manager at Conveyor Systems Limited (CSL) explores the vital role conveyor… Read more »
At LogiMAT this year Flexco Europe will showcase innovative solutions for safe belt conveyor… Read more »
The LOBO System, a leading provider of modular access solutions, has recently supported KNAPP,… Read more »
Nord Drivesystems has specially developed the MAXXDRIVE XT industrial gear unit for the requirements… Read more »
SICK has developed a versatile and easy to install Roller Sensor Bar to tackle… Read more »
Pepperl+Fuchs Factory Automation says its Contour2D sensor system enables optimally efficient detection of conveyor… Read more »
NORDAC FLEX frequency inverters from NORD DRIVESYSTEMS are true allrounders: They not only offer… Read more »
Beumer Group supplied a complex complete system composed of several belt conveyors to one… Read more »
Claire Umney has been appointed as managing director of Breathe Technologies to drive the… Read more »
Conveyor supplier, Conveya has recently added another product to its portfolio – the Flexible… Read more »
Dorner GmbH continues its product expansion by adding the 2200 Series Modular Belt Conveyor… Read more »
Bristol-based Coveya Ltd specialises in the design, manufacture and supply of conveyor systems &… Read more »
Dorner GmbH is expanding its presence throughout Europe by adding the 2200 Series LPZ… Read more »
Bristol based Coveya Ltd specialises in the design, manufacture and supply of conveyor systems… Read more »
Bremen-based conveyor technology specialist cellumation has been granted €2 million in EU funding for… Read more »
UK automation specialist Conveyor Networks is to partner with Geek+ to become an official… Read more »
Plastic Omnium are a global company whilst remaining an independent family-owned business, who are… Read more »
Swiss conveyor specialist Avancon has teamed up with South Korean system integrator Asetec to… Read more »
Automated conveying and roller specialist Interroll has named a new head of its innovation… Read more »
An innovative cellular conveying system is set to make its debut at LogiMAT in… Read more »
BÖWE SYSTEC has signed an agreement to take a majority stake in SGA Conveyor… Read more »
Innovative solutions for the fully automatic handling of pallets: With a new stacker crane… Read more »
Cimcorp, a manufacturer and integrator of turnkey robotic order fulfillment solutions, has signed an… Read more »
Rulmeca has launched its renewed TM400 motorized pulley generation. Thanks to optimized components, the… Read more »
Conveyor technology expert Interroll has reported strong annual growth figures for 2018. “The high… Read more »
Conveyor technology expert Interroll says it grew substantially in 2018. It reports that orders… Read more »
Logistics provider Dachser says it plans to replace all of its roughly 6,000 ground… Read more »
UK lighting and signal solutions provider i-vision has developed a stand-alone modular induct signal… Read more »
Honeywell has completed its acquisition of warehouse automation solutions provider Transnorm. Honeywell acquired the… Read more »
Leicester (UK)-based BS Handling Systems has installed an 18.5 metre long pallet roller conveyor… Read more »
Shuttle or trolley? In everyday parlance, a shuttle is understood to mean a vehicle… Read more »
Conveyor system specialist Interroll says it recorded strong organic first-half growth in sales revenue… Read more »
A new module has been added to the Interroll Modular Conveyor Platform (MCP). The… Read more »
Beumer Group has launched two start-ups that use advanced and disruptive business ideas to… Read more »
Nord Drivesystems has outlined its LogiMAT plans, saying it will present intelligent, versatile and… Read more »
The business of packaging is, at its core, involved in product and materials handling,… Read more »
Nerak Wiese is launching a range of spiral conveyors. Capable of handling a variety… Read more »
Egemin is expanding its EÂ’tow® in-floor chain conveyor product range with the new EÂ’tow®… Read more »
Throughout its 30-year history FB Chain has acted not only as a supplier to… Read more »
Everything under one roof. Swiss logistics company Schöni AG has spent the last two… Read more »
Renold has launched a new same-day despatch service for its range of BS conveyor… Read more »
DornerÂ’s 2200 Precision Move Pallet Systems are the latest advancement in pallet traffic management.… Read more »
The new 53 litre capacity BITOBOX XLmotion plastic containerÂ’s base features diagonal support ribbing.… Read more »