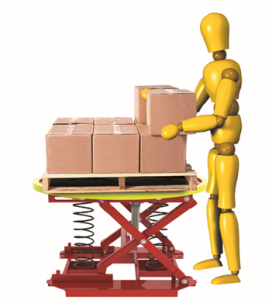
The PalletPal 360™ lifting technology has been launched in the UK by Marco Scissor… Read more »
The PalletPal 360™ lifting technology has been launched in the UK by Marco Scissor… Read more »
To help businesses challenged with handling pallets over loading plates, bumpy ground or on… Read more »
The oil and gas industry is getting ready for a new event: the first… Read more »
This is one of the most important times of the year to ensure that… Read more »
A loading bay application that helps carriers and companies manage collections and deliveries more… Read more »
Corporate storage and distribution company, Gillards Worldwide Warehousing and Distribution, has become one of… Read more »
Specialist loading bay equipment and industrial door manufacturer Stertil Dock & Door Products has… Read more »
An increase in the weight of deliveries has led BM Catalysts Ltd to invest… Read more »
Industrial door and loading bay equipment manufacturer Hörmann says it will display a selection… Read more »
TJ Hood Transport, the European haulage, distribution and warehousing operator has added a number… Read more »
Operators generally spend over 50%, and sometimes as much as 80%, of their time… Read more »
ACME Production Services, the event and entertainment transport specialists, have added two, high security… Read more »
Established in 2006 and already a major player in the Northern Ireland vehicle rental… Read more »
Thorworld, the leading supplier of loading and unloading equipment, has revealed there are a… Read more »
Thorworld Industries has installed three fixed loading bay solutions each comprising a ramp,… Read more »
Every year, there are over 5,000 accidents involving transport in the workplace, and despite… Read more »
Relocation from Germany to the UK has been the driving force behindUnifraxs decision to… Read more »
The new facility harnesses renewable energy and sustainable solutions, achieving BREEAM ‘Excellent’ and LEED… Read more »
FedEx has announced the opening of its newest facility in Vianen, the Netherlands. This… Read more »
Jan Tromp Transport Group has installed a Modular Rollerbed System with Powered Cargo Rollers… Read more »
The recently launched Combi-CB70E has earned global recognition for its ergonomic design, performance, and… Read more »
Schenk UK is proud to announce the successful start of a major long-term gas… Read more »
Powerful, high performance GV/GVR-Series of planetary gearboxes with rigidity for high radial load has… Read more »
GMR Safety, a global supplier of wheel restraint systems, is pleased to announce the… Read more »
If you’ve ever walked through the pasta aisle of your local supermarket, chances are… Read more »
As the logistics sector continues to evolve at pace, the demand for smarter, faster,… Read more »
Transparency of the global supply chain is becoming the weapon of choice for smart… Read more »
Data and energy transmission provider Conductix-Wampfler serves all parts of the warehouse and logistics… Read more »
Industrial doors from Efaflex lead the world because they combine premium manufacturing, super high-speed… Read more »
Experience and track record matter in freight forwarding, according to Paul Everley, Global Head… Read more »
Joloda Hydraroll has installed an automated air cargo handling system for Schiphol Express at… Read more »
Logistics companies face immense pressure to optimise their operations, enhance security, reduce losses, and… Read more »
Automated picking and handling operations often require the usage of more than one technology… Read more »
More and more BBQ enthusiasts are on fire for the products of the US… Read more »
With more than 15 years of expertise in the supply, installation, and maintenance of… Read more »
In April 2025, the European Commission announced new laws to update how road transport… Read more »
For most people, summer is the best time of year. It means days out… Read more »
The May 2025 issue of Logistics Business magazine: Insightful and unique content covering the… Read more »