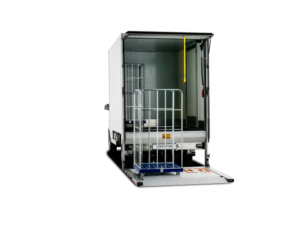
Cenntro Automotive Europe is introducing a tail lift variant for its Logistar 200 electric… Read more »
Cenntro Automotive Europe is introducing a tail lift variant for its Logistar 200 electric… Read more »
The RHA has published long-awaited guidance to improve safety around the use of tail… Read more »
Denmark’s first electric trucks have arrived, equipped with ZEPRO tail lifts supplied by Hiab.… Read more »
The Pallet Network (TPN) is introducing a per-pallet surcharge for all tail-lift deliveries, as… Read more »
La Cisa Trasporti Industriali S.r.l. (La Cisa) ordered a total of seven tailored forklift… Read more »
The best lift truck operators from across the UK and Ireland proved their skills… Read more »
The forklift truck Market Index produced by the British Industrial Truck Association (BITA) shows… Read more »
Major UK Fashion and Home retailer Next has turned to a 15m forklift to… Read more »
Intralogistics specialist Linde Material Handling (MH) has expanded its range of automated forklift and… Read more »
A British freight and logistics 3PL provider has praised the performance and reliability of… Read more »
Yale Lift Truck Technologies introduces the new ERP2.2-3.5N electric lift truck series, designed to… Read more »
In an interview with Stefan Budweit, President and CEO of Clark Europe, Peter MacLeod… Read more »
As Linde MH reinvents the role of the forklift to best service a smart,… Read more »
Today’s forklift industry experiences both as many changes as challenges. Over the last year… Read more »
Sarkany, one of the retailers in Argentina’s footwear sector, has integrated Mecalux’s Easy WMS… Read more »
Linde MH has launched new trucks into the popular one-to-two tonne sector. Peter MacLeod… Read more »
Clark has expanded the S-Series Electric with new three- and four-wheel forklifts. The new… Read more »
Junction 4 Pallets has bought two new Linde Evo H20 forklifts to add to… Read more »
Bobcat will be presenting two major new developments at LogiMAT 2025 as part of… Read more »
Don-Bur, British supplier of commercial vehicle bodywork, has delivered 16 newly designed 13.6m long… Read more »
Nationwide Platforms recently provided working at height support to Yusen Logistics (UK) for the… Read more »
Linde Material Handling (MH) is replacing its existing range of electric forklifts with a… Read more »
One of the most cost-effective and efficient ways to handle materials in the workplace… Read more »
Union Industries, one of the UK’s leading manufacturers of bespoke industrial doors, has assisted… Read more »
Yale Lift Truck Technologies has announced the expansion of its UX series of lift… Read more »
A new range of scissor lifts has been launched by Hörmann Transdek which are… Read more »
Companies can now manage large lift truck operator communities and their training records more… Read more »
Cimcorp is a pioneer in intralogistics solutions, simplifying material flows and improving customers’ profitability… Read more »
Briggs Equipment is proud to support the ambitions of businesses in the UK &… Read more »
ABM will present complete drive solutions for a wide range of intralogistics applications at… Read more »
With Yale Reliant, a package of advanced operator assistance systems, Yale Lift Truck Technologies… Read more »
By any measure, CareCo is a genuine success story. Built on energy, innovation and… Read more »
Yale Lift Truck Technologies has launched two specially engineered operator assistance options to support… Read more »
Warehouses are some of the most important parts of the way that retail organisations… Read more »
Hyundai Material Handling has unveiled a range of Heavy Line diesel forklift trucks, with… Read more »
Logisnext UK Ltd is delighted to announce that the brand UniCarriers is now replaced… Read more »
Baoli, the forklift manufacturer that is part of the KION Group, is launching a… Read more »
Kemi Shipping Oy, owned by Finnish Metsä Group, has ordered eight award-winning Konecranes E-VER… Read more »
Many companies are currently suffering from rising energy costs and are looking for additional… Read more »
BYD, a world-leading manufacturer of New Energy Vehicles (NEVs), is using the occasion of… Read more »
UniCarriers has launched a new generation of the ALR stand-in low lifter, now offering… Read more »
Clark‘s globally coveted S-Series celebrated its debut in 2018. With the special “Smart, Strong… Read more »
Forklifts and other industrial trucks have become essential work equipment in logistics and warehousing.… Read more »
Internal logistics control is still often based on pen and paper and print-outs from… Read more »