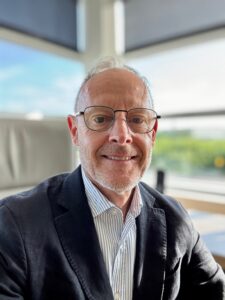
GMR Safety, a global supplier of wheel restraint systems, is pleased to announce the… Read more »
GMR Safety, a global supplier of wheel restraint systems, is pleased to announce the… Read more »
The handling of loaded containers in tight spaces has always been a logistical challenge.… Read more »
Hörmann UK have introduced a new Automatic Wheel-blocking system (AWB) for the ultimate in… Read more »
Following last year’s announcement, Trelleborg Wheel Systems is pleased to announce the acquisition by… Read more »
How can steering a forklift truck become even more ergonomic? Linde Material Handling provided… Read more »
Haulage wheel safety solution company Checkpoint has pioneered product innovation in its range of… Read more »
Reusable packaging innovator, Loadhog has recently launched wheeled Dollies which have been designed specifically… Read more »
The new 770-Litre wheeled bin a new product launch by Craemer has gained UN… Read more »
Wheel and castor specialist AUT has highlighted the ready stock it has available for… Read more »
With delays and blockages now starting to affect global supply chains due to the… Read more »
January 2020 is a significant milestone for AUT Wheels and Castors as they celebrate… Read more »
Due to customer demand and the vast range of products available, UK wheel and… Read more »
Clark has launched a new range of electric four-wheel forklift trucks capable of taking… Read more »
Trelleborg Wheel Systems has picked up two noteworthy accolades from Hyster-Yale Group, the ‘Excellence… Read more »
A technical report supplied by German wheel and castor manufacturer, Blickle: Whether it’s at… Read more »
TCM says the UK food and warehouse/distribution sector has hailed the forklift provider’s FB… Read more »
Wheel and castor specialist Blickle has extended its range of truck locks. These securely… Read more »
Wheel maker Blickle has launched a series aimed at the hygiene-priority market. The Blickle… Read more »
Wheel and castor maker Blickle has developed the new POES and ALES series for… Read more »
P3 Logistic Parks have unveiled a new factory and distribution centre in Bratislava, Slovakia… Read more »
Leading door manufacturer, Hörmann, has launched its first UK Wheelblocker – a new piece… Read more »
Camso, formerly Camoplast Solideal, says it has strengthened its service offering in Europe and… Read more »
The leading FMCG supply-chain operator, Fowler Welch, reports safe coupling across its fleet since… Read more »
Leading Netherlands haulier, HN Post & Zonen has taken delivery of the countrys first… Read more »
Personalised, predictive and always driveable. Tomorrows intelligent truck is more similar to a smartphone… Read more »
In Reality Road, Volvo Trucks TV series, a Volvo FH is subjected to a… Read more »
An innovative new scheme launched by Oldham Council to support people in warehouse work… Read more »
Global freight forwarder Woodland Group has inked a new three-year deal with automotive aftermarket… Read more »
Across freight, highways, and complex industrial environments, one quiet challenge creates delays, adds risk,… Read more »
Powerful, high performance GV/GVR-Series of planetary gearboxes with rigidity for high radial load has… Read more »
Tate & Lyle Sugars continue to push sustainability with the introduction of two brand-new… Read more »
As the logistics sector continues to evolve at pace, the demand for smarter, faster,… Read more »
Year Two of Bobcat’s ownership of the former Doosan forklift brand, and we’re starting… Read more »
As Linde MH reinvents the role of the forklift to best service a smart,… Read more »
Freight forwarders and logistics businesses will be able to see a game-changing transport management… Read more »
In the competitive world of industrial real estate, safety and flexibility are paramount. Network… Read more »
Accumulators and batteries containing lithium require highly sensitive handling in strict accordance with legislation.… Read more »
Life on the road can be unpredictable. For thousands of professional drivers crossing Europe… Read more »
Two specially modified and uniquely liveried Schmitz Cargobull S.KO COOL box-body semi-trailers have been unveiled… Read more »
With rising labour, fuel and packaging costs, many companies today are seeking solutions that… Read more »
GMR Safety, designer and manufacturer of wheel restraint systems for loading docks is introducing… Read more »
Bobcat Company is showcasing two new forklifts which offer industry-leading features at ProMat 2025,… Read more »