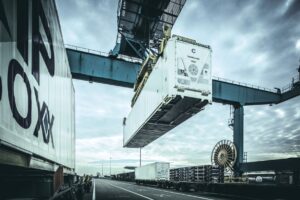
Thermo King, a leader in transport temperature control solutions and a brand of Trane… Read more »
Thermo King, a leader in transport temperature control solutions and a brand of Trane… Read more »
Thermo King, a leader in transport temperature control solutions, has unveiled three new breakthrough… Read more »
Thermo King, a leader in transport temperature control solutions, announced – and will feature… Read more »
Thermo King has announced its new UT-R undermount refrigeration systems, which will be a… Read more »
Thermo King has launched a new research and development (R&D) centre adjacent to its… Read more »
Thermo King, a leader in transport temperature control solutions, has supplied 950 of its… Read more »
Thermo King, a leader in transport temperature control solutions, is exhibiting at the ITT… Read more »
Thermo King, a leader in transport temperature control solutions, has been awarded the global… Read more »
Thermo King, a global leader in intelligent end-to-end temperature-controlled cold chain solutions, and its… Read more »
Thermo King, a leader in transport temperature control solutions, has approved the use of… Read more »
Thermo King, a leader in transport temperature control solutions and a brand of Trane… Read more »
Thermo King has launched its new lithium-ion (Li-ion) battery for refrigerated transport. The battery… Read more »
Thermo King has today launched premier+, an all-in-one flexible financial solution featuring a fully… Read more »
With fully variable airflow, unrivalled fuel efficiency, and a significantly lowered cost of ownership,… Read more »
Thermo King and BPW announced today the collaboration of both companies to develop a… Read more »
Three German transport and logistics companies specializing in moving temperature sensitive fresh food products… Read more »
Tesco, the largest retailer in the United Kingdom (UK) and one of the world’s… Read more »
Vehicle refrigeration specialist Thermo King says that its new, fully electric E-200 multi temperature… Read more »
Ingersoll Rand-owned brands Thermo King and Frigoblock will discuss the future of refrigerated transport… Read more »
The CV Show 2019 showcase from Thermo King and Frigoblock is to feature their… Read more »
Transport Solution businesses Thermo King and Frigoblock of Ingersoll Rand, a world leader in… Read more »
Thermo King®, a leader in transport temperature control solutions for a variety of mobile… Read more »
The Galway, Ireland manufacturing facility of Thermo King®, a manufacturer of transport temperature control… Read more »
Transportation solution businesses Thermo King and FRIGOBLOCK, of Ingersoll Rand, will welcome visitors at… Read more »
Thermo King, manufacturer of transport temperature control solutions, will equip the new Hamad Port… Read more »
Thermo King, a manufacturer of transport temperature control solutions for a variety of mobile… Read more »
Thermo King, a manufacturer of transport temperature control solutions for a variety of mobile… Read more »
Transportation solution businesses Thermo King and FRIGOBLOCK of Ingersoll Rand, a world leader in… Read more »
At the Intermodal Europe show in Hamburg, Germany, Thermo King, a manufacturer of transport… Read more »
Thermo King, a manufacturer of transport temperature control solutions for a variety of mobile… Read more »
Thermo King, a manufacturer of transport temperature control solutions for a variety of mobile… Read more »
Thermo King, a manufacturer of transport temperature control solutions for a variety of mobile… Read more »
Musgrave Wholesale Partners, the market leader in Ireland for multi-temperature food delivery service to… Read more »
Thermo King, a manufacturer of transport temperature control solutions for a variety of mobile… Read more »
Thermo King a manufacturer of transport temperature control solutions for a variety of mobile… Read more »
Ingersoll Rand has created the EcoWise portfolio of products for its climate and industrial… Read more »
Food service, catering, hotels, grocery and pharmaceutical delivery companies are just a few businesses… Read more »
Thermo King a manufacturer of transport temperature control solutions for a variety of mobile… Read more »
Farmexim, one of the largest distributors of pharmaceutical products in Romania, works with Thermo… Read more »
Thermo King, a manufacturer of transport temperature control solutions for a variety of mobile… Read more »
Visit Thermo King at the stand A-01 in Hall 7.1a of the FRUIT LOGISTICA… Read more »
Today Thermo King, a manufacturer of transport temperature control solutions for a variety of… Read more »
Nationwide Platforms recently provided working at height support to Yusen Logistics (UK) for the… Read more »
Peak season 2023 was challenging for retailers. Cost of living concerns dented consumer confidence,… Read more »