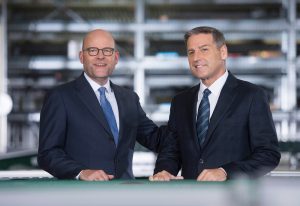
Starting a new chapter in the global supply chain industry, the KION Group has… Read more »
Starting a new chapter in the global supply chain industry, the KION Group has… Read more »
DK Group whose subsidiary businesses include the logistics solutions specialists DK Fulfilment Ltd… Read more »
CSafe Global has confirmed completion of the acquisition of Kalibox. With two manufacturing locations… Read more »
Honeywell says it has completed its $1.5 billion acquisition of Intelligrated, a privately held… Read more »
UK manufacturer Rosewood Packaging has acquired Scott Packagings Manchester business for an undisclosed sum.… Read more »
Trelleborg has finalized the acquisition of CGS Holding a.s. a privately-owned company with… Read more »
The Rhenus Group has acquired Swiss project logistics specialist KOG Worldwide AG. KOG Worldwide… Read more »
FedEx Corporation and TNT Express hereby jointly announce that they have obtained the unconditional… Read more »
The GEFCO Group, a global player in logistics for manufacturers and the European leader… Read more »
It is important for vendors to make a financial model in order to get… Read more »
GBA Logistics, a provider of logistics solutions, proudly announces the acquisition of The Silver… Read more »
Unlocking customer experience is the critical role of your supply chain, writes Roy Arguelles,… Read more »
Wincanton Logistics Directors are now supporting a £762m takeover offer from the American third… Read more »
The Bolloré Group and the CMA CGM Group announce the completion today of the… Read more »
Stansted Airport in Essex is FedEx’s biggest cargo hub in Britain. David Priestman grabbed… Read more »
Geodis has pledged to reduce its scope 1 and 2 greenhouse gas (GHG) emissions… Read more »
Dexory, a leading provider of cutting-edge AI and robotics solutions, and ID Logistics have… Read more »
Joloda Hydraroll Ltd, global loading and unloading solutions specialist, has today announced its acquisition… Read more »
J. & J. Denholm Limited (the Denholm Group) is excited to announce that Denholm… Read more »
Joloda Hydraroll, a company that specialises in trailer loading and unloading solutions, has been… Read more »
Cain International, a privately held investment firm, has completed the development phase of its… Read more »
SRT Group, parent company of leading last-mile specialist delivery platform Stuart, announced on Thursday,… Read more »
Can warehouse automation advance sustainability? Dan Migliozzi, Head of Sales at independent systems integrator,… Read more »
Koerber Supply Chain’s ‘Elevate’ event in Prague was an opportunity to discover how software… Read more »
Re-brands are sensitive and critical operations and the warehouse automation sector is no exception.… Read more »
Today, Aptean, a global provider of mission-critical enterprise software solutions, announced its acquisition of… Read more »
Otonomi, specialist in innovative supply chain risk technology and the freight insurance industry, has… Read more »
AXA IM Alts, a global leader in alternative investments with over €185 billion of… Read more »
Southgate Global, formerly known as Southgate Packaging, has announced a repositioning to communicate its… Read more »
Continental has acquired Kinexon’s specialist division for on-board operating systems for the intelligent control… Read more »
St. Modwen Logistics (“St. Modwen”), one of the UK’s leading logistics developers and managers… Read more »
DTZ Investors has completed the acquisition of Coventry Logistics Park for £140,415,000, one of… Read more »
What brings you back to your favourite online retailer? Other than product quality and… Read more »
Howard Tenens Logistics are pleased to have been awarded a new contract with Beavertown… Read more »
In view of the global trend of omni-sourcing, DHL Supply Chain, the world’s leading… Read more »
Prologis, the UK’s leading owner and developer of logistics property, has announced two changes… Read more »
At the SPS manufacturing event in Parma, Italy, Bonfiglioli presented technologies including its mechatronic… Read more »
When it comes to manufacturing high-quality fashion, Walbusch Group relies on Polymax Group, among… Read more »
Following last year’s announcement, Trelleborg Wheel Systems is pleased to announce the acquisition by… Read more »
Lödige Industries, a leading provider of logistics systems, is significantly expanding its capacities in… Read more »
For the expansion of their existing logistics infrastructure, retailers have for a long time… Read more »