Cost-efficient Brownfield, Retrofit Solutions
17th May 2023
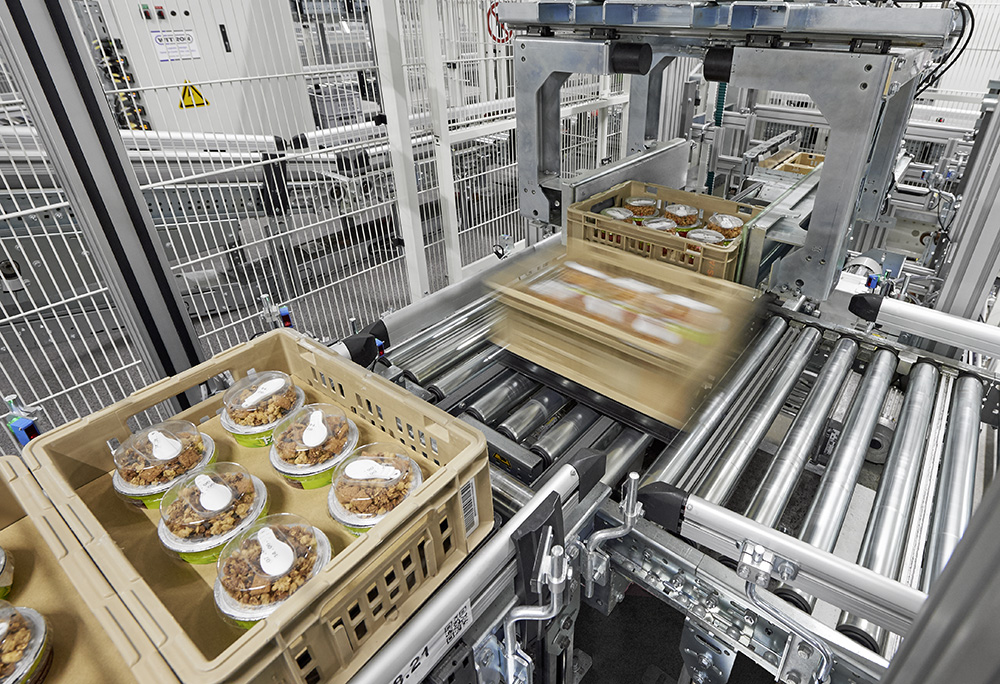
For the expansion of their existing logistics infrastructure, retailers have for a long time mainly preferred greenfield solutions over brownfield, says Witron. There is currently a trend on the market, both nationally and internationally, for brownfield solutions – i.e., the integration of new technology into existing buildings – to become increasingly attractive and a viable addition to the greenfield strategy. Specifically, this can involve both modernizations and expansions of technology and building. Consequently, it is a matter of transforming facilities that were previously used manually into automated logistics centres.
True to the credo ‘use your assets’, there are many factors that speak in favour of making existing logistics structures fit for the future within a brownfield strategy and thus saving money and time. The advantages of a brownfield strategy are versatile:
• The existing distribution centre is already at the right location
and is logistically well-integrated into the retail network in terms of stores and suppliers – with a good connection to the traffic route and rail network. The energy and communication systems are already in place and employees already come from the region – an enormous advantage in terms of retaining know-how, corporate culture, and recruiting.
• It is difficult to obtain new land for greenfield solutions
New building land is becoming scarce, as many communities are designating fewer and fewer commercial property due to their sustainability strategies. In addition, the brownfield logistics center already exists and often provides additional neighbouring expansion areas.
• New commercial real estate and new buildings are expensive
Both the acquisition of the property, its infrastructure, as well as the actual construction work cost money – currently with permanently rising costs for land, material, and craftspeople. In addition, any marketing of existing real estate is completely eliminated.
• The construction of a new building is a time factor
A brownfield solution can be utilized more quickly because it eliminates the time needed to find land, obtain permits, plan constructions, and erect the building.
• Implementing state-of-the-art technology into an existing building is
cost-efficient – whether by modernizing already existing components (racking systems, mechanics, conveyor systems, PLC + IT) or by completely integrating new innovative storage and picking solutions. The result is another positive cost and time factor.
• In terms of a holistic sustainability strategy, the reuse of existing assets is a decisive factor in avoiding land sealing or other waste of resources – economically, ecologically, and socially.
End-to-end implementation concept required
In order to evaluate whether the existing logistics facility is suitable for the future strategic approach, the first step is to obtain a thorough analysis and an end-to-end implementation concept. This includes:
• The verification of the existing building structure / building fabric
Depending on the temperature zone, e. g. floor conditions, statics, clear height, technical building equipment including air-conditioning technology, available building areas, possible expansion areas, possible building expansions, etc.
• The extent to which existing logistics technology can be modernized or is replaced, complemented by new logistics technology (e.g., OPM, AIO, ATS, GTP, shipping buffer, highly dynamic stacker cranes, and conveyor system, etc.)
• The design of material flow processes
In addition to the optimal connection of all logistics areas and temperature zones, typical building requirements are also being considered. These include, for example, good accessibility for service and maintenance teams, cleaning of the facility, fire protection, escape routes, or how the new technology can be physically implemented into the building in the best way (e.g., via the roof or by opening side walls).
• The transformation process – meaning how the commissioning processes are implemented in terms of organization, timing, and technology.
This requires an end-to-end change strategy (including installation and modernization cycles, dismantling phases, transition concepts with scenarios for temporary local relocation of existing business operations, pro-active backup scenarios, etc.). In the process, the most important question has to be clearly addressed: How will the project be implemented throughout the entire project phase – and how will the ongoing operation or delivery to stores and consumers take place at the same time. Depending on the individual case, it is possible to use different approaches to implement this in a practical way either at the site or in the logistics network.
Brownfield references worldwide
WITRON experts are very familiar with the requirement to economically map brownfield solutions with automated storage and picking technology. The company is considered one of the global market leaders in the design, implementation, maintenance, and system operation of highly dynamic distribution centres. Since the company’s foundation more than 50 years ago, 2,000+ projects have been successfully implemented – including more than 100 highly efficient logistics centres especially for food retailers throughout Europe, North America, and Australia. More than 30 percent of these are brownfield solutions.
COOP in Norway, for example, has increased the output of its dry, fresh, and frozen food areas by 30 percent during ongoing operations at its multi-temperature distribution centre in Oslo by installing eleven additional COM machines, including corresponding infrastructure such as further pallet storage aisles, tray storage aisles, stacker cranes, stretch-wrappers, de-palletizers, and conveyors, and now picks more than 625,000 cases daily.
For the Swiss food retailer MIGROS in Neuendorf, WITRON integrated a completely new logistics system into an operational distribution centre during ongoing operations and transformed it into a fully functional omni-channel distribution centre together with the existing facility. For this purpose, WITRON has installed a highly dynamic automated case and piece picking solution (OPM + AIO), and modernized, as well as optimized already existing logistics areas (receiving, shipping, e-commerce area), mechanical elements (high bay warehouse, conveyor systems), IT, and material flow processes. The system is currently designed for a daily pick performance of 472,000 cases and supplies 700 stores, as well as many thousands of home shopping customers in Switzerland from a range of more than 100,000 different items per year. The existing building in Neuendorf was complemented by a state-of-the-art, fully automated frozen food warehouse with WITRON OPM technology, which supplies 1,400 stores daily with more than 100,000 cases in a store-friendly manner. Order picking is done on both pallets and roll containers.
In addition, MIGROS replaced a completely manual convenience solution with a highly automated WITRON system (OPM, DPS, ATS) at its existing building in Suhr to stack goods onto pallets, roll containers, and into totes. This was preceded by the modernization of the dry goods logistics processes, which included the installation of a fully automated picking system with 28 COM machines on the roof of the existing distribution centre as part of the “Future COM” project. A masterpiece in terms of both technology and architecture. This site now supplies a total of 600 stores and 300 shops (kiosks, gas stations, etc.) with more than 430,000 cases daily.
The Spanish omni-channel retailer Condis in Montcada uses an existing manual high bay warehouse to supply a WITRON OPM system with goods.
French food retailers such as Diapar, E.Leclerc, and Intermarché also rely on WITRON’s brownfield experience. In North America, economic solutions were integrated end-to-end into the existing building structure for customers such as Albertsons, Kroger, and Sobeys.