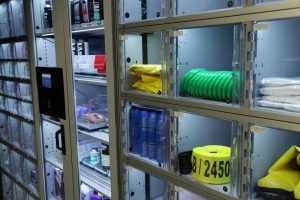
UK-based materials handling technology specialist, Narrow Aisle Ltd, will highlight its extensive range of intralogistics solutions when it exhibits alongside other logistics and supply chain specialists on the UKWA Pavilion at this years Multimodal.
Visitors will be able to discuss the FlexiPiCK a layer quantity customer order picking system that typically allows over 1100 cases per hour to be mechanically picked by one operator.
The FlexiPiCK allows users to take advantage of the increasingly popular layer quantity order picking concept pioneered in the USA – but without the need to invest in high fixed cost guided or automated handling technology that previous layer picking systems have relied upon.
The Flexi StorMAX system, yet another new concept in space saving storage solutions from Narrow Aisle, will also be highlighted.
The StorMAX is a warehouse management system-based (WMS) storage solution that, in comparison with storage systems served by conventional reach trucks, allows an amazing 50 per cent more pallet locations to be achieved within the dimensions of a store.
A company synonymous with high quality, ultra-efficient products, Narrow Aisle has earned a reputation for exceptional build reliability and customer service across the world and visitors to Multimodal can find out more by making their way to the Narrow Aisle stand.
www.flexi.co.uk
European regulators have been alarmed by the disproportionate share of CO2 trucks generate despite the fact they make up only 5% of the total traffic on European roads. CO2 emissions have continued to rise since the 1990s due to increasing road freight traffic and this issue is currently being discussed by EU leaders, who are focusing on measuring and reporting fuel consumption as a first step to cap CO2 emissions from heavy-duty vehicles,to see more please click here.
Cronus Logistics, one of the most innovative supply chain companies on the Irish-UK gateway understands the importance of reducing the amount of time spent travelling on UK and Irish roads and they are ahead of the curve in establishing their linehaul services.
Cronus Logistics has created an innovative service built on realising the importance of reducing road miles, driver hours, costs and cutting CO2 emissions. Pressure to lower emissions is mounting on manufacturers. There is currently no official method to measuring CO2 emissions from heavy-duty vehicles. As a step towards enforcing regulations the European Commission is introducing a Vehicle Energy Consumption Calculation Tool (VECTO) – a computer simulation measurement system that is expected to become mandatory as of this summer.
This is meant to be the first step in regulating emissions, however there are already concerns that VECTO won’t be effective due to the fact that there are so many different trucks on the market, making the industry too complex to be measured in this way. Rather than enforcing legislation that may not work in practice, by actually reducing the amount of time travelling on roads Cronus Logistics has tackled the problem head on.
Cronus Logistics is the only Irish Sea logistics company offering a comprehensive door-to-door service for dry freight, with full control of every element of the supply chain. This culminates in a reliable, competitive and green route to market.
Cronus has recently increased their services based on this ethos utilising two dedicated gateways – Bristol to Warrenpoint and Cardiff to Dublin. By linking these four ports they can strengthen the offerings to core manufacturing sectors to offer reduced road miles, lower CO2 emissions and tailored deliveries to customer requirements, alongside maintaining an industry standard 48 hour service.
If you want a service that demonstrates green credentials and saves on costs, Cronus is the logistics solution that reduces road miles, cuts CO2 emissions and contributes to a stronger financial bottom line.
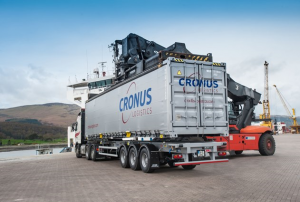
Cronus Logistics, one of the most innovative supply chain companies on the Irish-UK gateway understands the importance of reducing the amount of time spent travelling on UK and Irish roads and they are ahead of the curve in establishing their linehaul services.
Cronus Logistics has created an innovative service built on realising the importance of reducing road miles, driver hours, costs and cutting CO2 emissions. Pressure to lower emissions is mounting on manufacturers. There is currently no official method to measuring CO2 emissions from heavy-duty vehicles. As a step towards enforcing regulations the European Commission is introducing a Vehicle Energy Consumption Calculation Tool (VECTO) – a computer simulation measurement system that is expected to become mandatory as of this summer.
This is meant to be the first step in regulating emissions, however there are already concerns that VECTO won’t be effective due to the fact that there are so many different trucks on the market, making the industry too complex to be measured in this way. Rather than enforcing legislation that may not work in practice, by actually reducing the amount of time travelling on roads Cronus Logistics has tackled the problem head on.
Cronus Logistics is the only Irish Sea logistics company offering a comprehensive door-to-door service for dry freight, with full control of every element of the supply chain. This culminates in a reliable, competitive and green route to market.
Cronus has recently increased their services based on this ethos utilising two dedicated gateways – Bristol to Warrenpoint and Cardiff to Dublin. By linking these four ports they can strengthen the offerings to core manufacturing sectors to offer reduced road miles, lower CO2 emissions and tailored deliveries to customer requirements, alongside maintaining an industry standard 48 hour service.
If you want a service that demonstrates green credentials and saves on costs, Cronus is the logistics solution that reduces road miles, cuts CO2 emissions and contributes to a stronger financial bottom line."/>
Supply Chain Salary Levels Set To Rise 5% in 2016

The results of the Robert Walters Salary Survey have shown that salaries for supply… Read more »
Supply Chain Efficiencies For UK Frozen Food Retailer
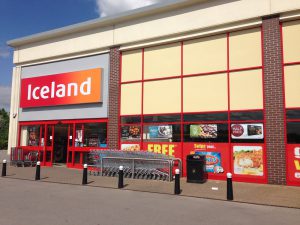
UK frozen food retailer Iceland has signed a new three-year commercial agreement with CHEP,… Read more »
New UK network to boost flexibility for Supply Chain Provider

The new network will improve our IT capabilities says Simon Calver, Yusen Logistics (UK)… Read more »
Date For European Supply Chain Day 2016 Announced

European Supply Chain Day 2016 is confirmed to take place on Thursday 21st April.… Read more »
Solutions That Move Supply Chains
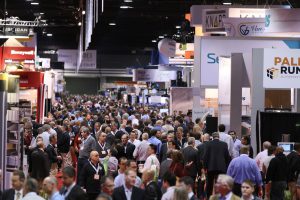
Name of Show: MODEX 2016 Show Sponsor: Material Handling Industry America (MHI) (www.mhi.org) Show… Read more »
Supply chain specialist and Fifth Wheel supplier make the perfect couple

The leading FMCG supply-chain operator, Fowler Welch, reports safe coupling across its fleet since… Read more »
Menlo Supports Academic Achievement in Supply Chain Management

Menlo Logistics (Menlo), the global logistics subsidiary of Con-way Inc. (NYSE: CNW), is continuing… Read more »
Polishing up Nailberrys supply chain
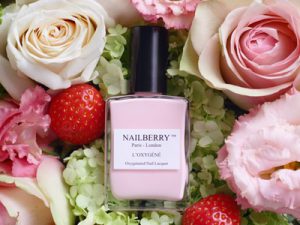
Walker Logistics, the specialist supply chain services operator, has commenced storing and distributing the… Read more »
Accenture Acquires Total Logistics, Adding Powerful Management Consulting and Technology Consulting Capabilities in Retail Supply Chain and Logistics
Accenture (NYSE: ACN) has acquired Total Logistics, an independent logistics and supply chain consultancy… Read more »
Calais Crisis Highlights Britains Supply Chain Achilles Heel
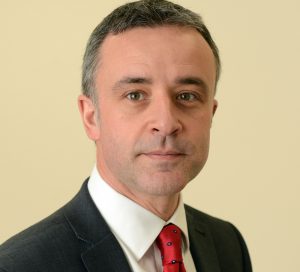
The topography of the Kent coastline may physically resemble the foot of England, but… Read more »
Suttons win supply chain management contract in Singapore
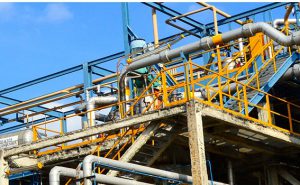
Chemical logistics and supply chain company Suttons has been awarded a supply chain management… Read more »
TRAVIS PERKINS PLC AND CHEP SET TO MODERNISE SUPPLY CHAIN WITHIN THE CONSTRUCTION INDUSTRY IN THE UK
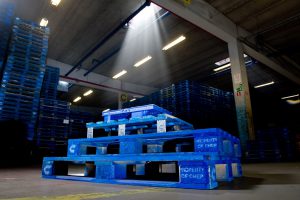
Travis Perkins plc, one of the largest suppliers to the UK building and construction… Read more »
New Container Logistics service to boost revenues for Advanced Supply Chain

A fast growing logistics firm is expecting a new service to generate revenues of… Read more »
Links connect port to automotive supply chain

Port of Sunderland has seen rail lines that had been out of use for… Read more »
Antalis to present its latest packaging solutions to achieve operational excellence throughout the packaging supply chain
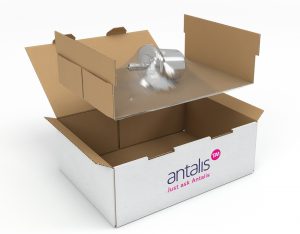
Operational excellence throughout the packaging supply chain will be the overarching theme for Antalis… Read more »
Plastic export pallets take costs out of the supply chain
Over the past decade there has been a steep decline in air cargo volume… Read more »
Supply chain risk jumps to nine month high as supply chains are rocked by the collapse in commodity prices

The CIPS Risk Index reversed its improving trend, moving to 78.2 in Q4 2014… Read more »
SMART LABELS COULD ERADICATE WASTE FROM FRESH FOOD GLOBAL SUPPLY CHAIN
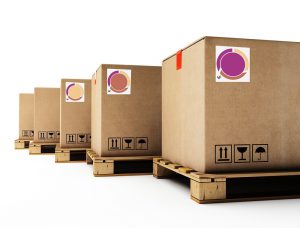
Insignia Technologies, Scotlands leading intelligent packaging company, announced today the launch of the Stock… Read more »
ORBCOMM Improves Cold Chain Telematics
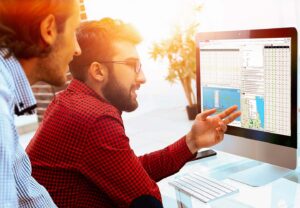
ORBCOMM Inc., a leading global provider of supply chain IoT technology, is leveraging its… Read more »
AddSecure Partnership with Cold Chain Federation
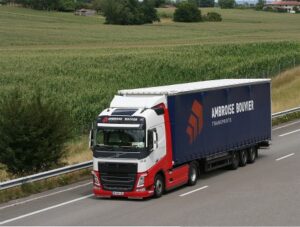
AddSecure, a European provider of secure IoT connectivity and end-to-end solutions such as temperature-monitoring… Read more »
Cold Robots for Cold Chain Logistics
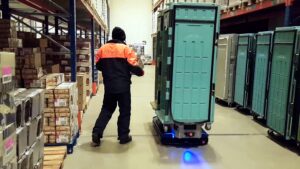
Autonomous Mobile Robots will contribute significantly to efficient and productive use of increasingly vital… Read more »
Distribution, not supply, is creating global food insecurity
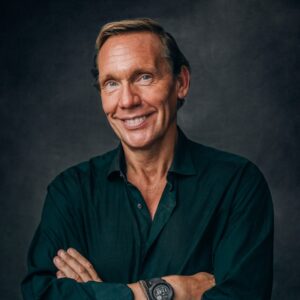
The pandemic, followed by a brutal war in Ukraine, has provided a catch-all explanation… Read more »
o9 Solutions launches Supply Sensing

o9 Solutions, a leading enterprise AI software platform provider for transforming planning and decision-making, has… Read more »
Cold Chains can Save Lives
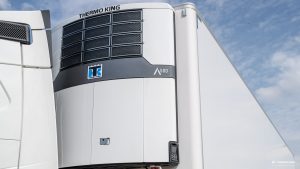
The launch of the COVID-19 vaccination campaign in December 2020 led to great relief… Read more »
Blockchain technology as a transformational force
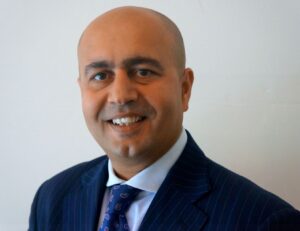
The global logistics industry, worth $8.5tn, is the backbone of economies and thriving commerce,… Read more »
White paper: pharma cold chain technologies compared
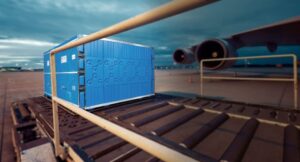
The vital role that temperature-controlled packaging plays in transporting pharmaceuticals around the world has… Read more »
Tower takes cold chain containers on the road
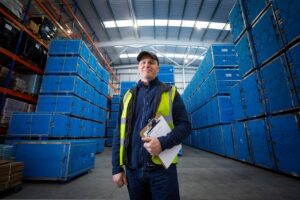
In its first appearance at the renowned LogiPharma conference, Tower Cold Chain is speaking… Read more »
Smart item supply, engagement & authentication with dual-frequency RFID labels
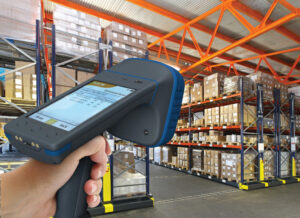
Brady Corporation presents a new, highly reliable dual-frequency RFID label that combines the advantages… Read more »
Transporeon acquires SupplyStack and Nexogen
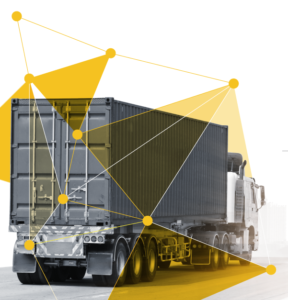
With the acquisition of SupplyStack and Nexogen, Transporeon customers profit once more from the fact… Read more »
Tower Cold Chain launches new brand identity
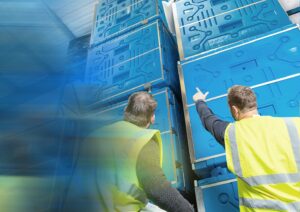
Pharmaceutical thermal protection specialist Tower Cold Chain has launched a new brand identity, supported… Read more »
New approach needed to secure cold chain workforce
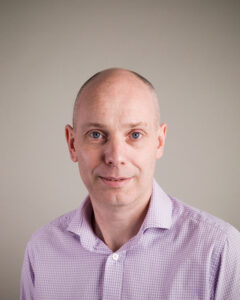
A new approach is needed to secure cold chain skills for the future and… Read more »
New guide helps businesses manage cold chain food safety
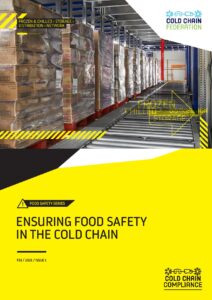
The Cold Chain Federation has published Ensuring Food Safety in the Cold Chain, the… Read more »
Blockchain Transaction Capacity and Speed Boost for Shippers

Complete supply chain transparency, unprecedented security, and the transactional capacity to serve the needs… Read more »
Spanish Supermarket Chain Automates Fresh Produce Distribution with Cimcorp
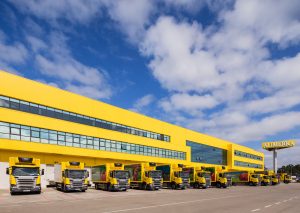
Automated fulfilment specialist Cimcorp has received an order to automate the distribution of fresh… Read more »
GDP Certification for Duisburg Cold Chain Specialist
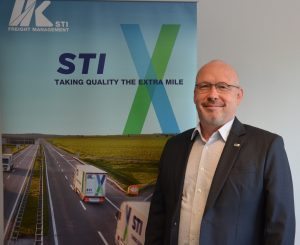
STI (Deutschland) GmbH, a subsidiary of STI Freight Management GmbH, has received GDP certification.… Read more »
“NO Plastic Pallet Supply Issues Post-Brexit” says UK Specialist
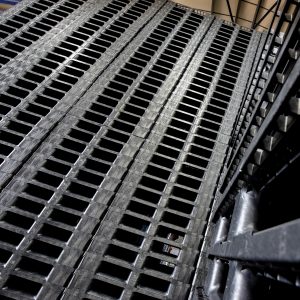
Plastic pallet specialist Jim Hardisty of goplasticpallets.com has reassured customers and exporters that there… Read more »