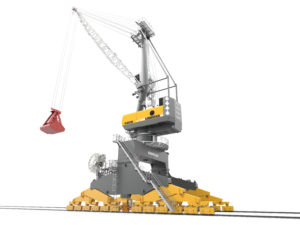
Liebherr has launched its first 100% electric portal crane. The Rostock-based manufacturer says that… Read more »
Liebherr has launched its first 100% electric portal crane. The Rostock-based manufacturer says that… Read more »
Daimler Trucks has handed over the world’s first all-electric light-duty (7.5-tonne) truck in series… Read more »
Leasing specialist Alphabet International says its operational lease portfolio grew by 5.5%, to 680,000… Read more »
Renault Trucks has announced that it will launch a range of electric vehicles in… Read more »
A case study presented by Doosan Industrial Vehicles: In autumn 2017, Münster-based Doosan Dealer… Read more »
Hiab, part of Cargotec, presented the world’s first electric powered skiploader concept vehicle at… Read more »
UK based distributor and supply chain specialist Westcoast Retail has signed a UK-wide deal… Read more »
Combilift has unveiled a new all-wheel drive, electric, multi-directional counterbalance forklift truck, with a… Read more »
Yale Europe Materials Handling is launching an 8 tonne lithium-ion counterbalance truck. The new… Read more »
Covers is a family owned timber and builders merchants operating a network of 13… Read more »
UK 3PL Bowker Group has added a fleet of five new Flexi articulated warehouse… Read more »
Logistics specialist Menzies Distribution has acquired London-based Gnewt Cargo, an all-electric delivery provider, for… Read more »
Royal Mail is to trial nine British-made fully electric commercial vehicles this month in… Read more »
Crown has launched the WP 3010 electric pallet truck, extending the forklift manufacturer’s well-established… Read more »
Derbyshire-based electric tug manufacturer MasterMover has signed a partnership with offshore lifting specialist Safelift… Read more »
Logistics management firm Wincanton has rolled out a new electric dairy tanker to serve… Read more »
Tevva Motors has officially opened the order books to owners and operators for its… Read more »
The Cartwright Group, a commercial vehicle bodybuilder and trailer manufacturer, aims to improve production… Read more »
Yale has announced a change to the specification of its 3-wheel ERP15-20VT series, which… Read more »
Crown, one of the worlds largest material handling companies, extended its electric counterbalance lift… Read more »
Hiab, part of Cargotec, has sold three MOFFETT E4 20.1 truck-mounted forklifts to FPS… Read more »
Doosan Industrial Vehicle UK has launched its new range of 1.5 to 2.0 tonne… Read more »
Crown, one of the worlds largest material handling companies, extended its electric counterbalance lift… Read more »
DHL, the worlds leading logistics provider, today announced the successful delivery of 40 electric… Read more »
Doosan Industrial Vehicle has begun production of a completely redesigned range of 1.5 and… Read more »
Kalmar, part of Cargotec, has signed a second repeat order for additional nine all-electric… Read more »
The automotive industry’s reliance on its supply chain running smoothly is important to ensure… Read more »
DHL Supply Chain has been appointed by bp pulse in a new warehousing and… Read more »
The logistics sector is actively seeking sustainable solutions to environmental challenges. But what are… Read more »
HUBTEX is expanding its MaxX series with a new model – the MaxX 60… Read more »
FarEye, a global last-mile technology platform, hosted the Last-Mile Leaders Event on April 19th… Read more »
Webfleet, Bridgestone’s global fleet management solution, has launched the EV Transition Tool to support… Read more »
With Schauer Gabelstapler GmbH, Clark Europe has brought a new sales partner for Austria… Read more »
First Exhibitors Announced for IAA TRANSPORTATION 2024: Leading Companies to Showcase Solutions Towards Climate… Read more »
By 2050, Europe should be the first CO2-neutral continent – that is the goal… Read more »
Less complexity, fewer variants, more efficiency, more power and simpler, faster commissioning, and maintenance.… Read more »
IKEA Ireland is today opening its state-of-the-art distribution centre in Rathcoole, Co. Dublin, marking… Read more »
Trane Technologies, parent company of Thermo King, reinforced the essential need to decarbonize and… Read more »