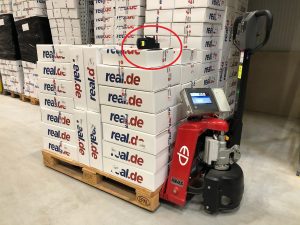
As the uptake of autonomous solutions increases in warehouses, integrated mobile weighing specialist Ravas… Read more »
As the uptake of autonomous solutions increases in warehouses, integrated mobile weighing specialist Ravas… Read more »
The Lifter by Pramac mobile weighing range offers many solutions designed to weigh anywhere… Read more »
RAVAS, a specialist in mobile weighing solutions, recently launched an update of the RAVAS… Read more »
Smart attachments like Ravas iForks demonstrate how to shift forklift value away from mere… Read more »
B&B Attachments announced as exclusive distributor for Griptech mobile weighing products in England and… Read more »
Mobile weighing specialist RAVAS, best known for its iForks product, has bought Ohio-based LTS… Read more »
Industrial weighing manufacturer Avery Weigh-Tronix has celebrated 200 years of innovation with a ‘Best… Read more »
Avery Weigh-Tronix has launched a new ‘Revenue Protection’ solution which can quickly and accurately… Read more »
Weighing solutions specialist Avery Weigh-Tronix has unveiled Uptime Select – a brand new range of… Read more »
In readiness for the IMO SOLAS Verified Gross Mass (VGM) requirements, which come into… Read more »
The Port of Felixstowe (UK) has confirmed that it will offer a container weighing… Read more »
B&B Attachments, the UKÂ’s leading supplier of fork lift truck attachments has had a… Read more »
With the ever increasing focus on productivity and safe-loading, the new LIFTLOG 1000 is… Read more »
Autonomous mobile robots optimise the movement of goods in warehouses, logistics centres and manufacturing… Read more »
Joloda Hydraroll has installed an automated air cargo handling system for Schiphol Express at… Read more »
How can warehouse AMR robots achieve orderly collaboration on a multi-machine scale? How do… Read more »
The team at goplasticpallets, a British provider of sustainable plastic pallets and boxes, is… Read more »
In a strategic partnership that aims to redefine sustainable industry, global recycling giant GEM… Read more »
LoadPlate® semi-automated loading solution by Actiw, a subsidiary of The Joloda Hydraroll Group, has… Read more »
Papick, ItPick and Depax are the robotics solutions dedicated to the logistics and forwarding sector… Read more »
The rise in Employer National Insurance in the UK is but one factor set… Read more »
LogiMAT 2025 is once again filling over 120,000 square metres in all ten exhibit… Read more »
Is reshoring right, asks Paul Cooper, director and industrial manufacturing specialist at management consultancy… Read more »
The November 2024 issue of Logistics Business magazine: Exclusive content spanning the international supply… Read more »
Ecommerce fulfilment is prone to frequent and often dramatic spikes in demand, and this… Read more »
Jungheinrich, RAVAS EUROPE, SAFELOG with Mercedes, SSI Schäfer and STILL have been announced as… Read more »
In December 2023 alone, £45 billion worth of goods were imported to the UK… Read more »
Itoh Denki, a leading international specialist in motorised drive roller (MDR) based material handling… Read more »
Companies aiming to improve their competitiveness through more highly automated intralogistics will find everything… Read more »
Exhibitors from nearly every sector of the industry are coming to LogiMAT 2024 to… Read more »
Lödige Industries, a global supplier of logistics systems, has recently completed the installation of… Read more »
Although any building that stores raw materials or manufactured goods before distribution is called… Read more »
When considering automated warehousing, stacker cranes have often been the default storage and retrieval… Read more »
You can just hear each other while Mikropakket’s 50-metre-long electrically powered sorting belt rapidly… Read more »
Customized solutions designed primarily for either indoor or outdoor use can now be implemented… Read more »
Dematic has recently completed commissioning of an automation project featuring innovative warehouse technology for… Read more »
James and James is a third party logistics (3PL) business set up for multiple… Read more »
A new, ultra energy-efficient, robot-based tote handling solution from LiBiao Robotics is launched today… Read more »
With covers made from locally sourced wood, the new generation of Stingray shuttle saves… Read more »
Some two years after introducing LiBiao robotic parcel sortation technology at its sorting centre… Read more »
Our penultimate look at all the finalists ahead of the IFOY Awards ceremony in… Read more »
The amount of industrial space taken up by manufacturers in key European markets is… Read more »
As we move inexorably towards the moment when the IFOY Awards are handed out… Read more »