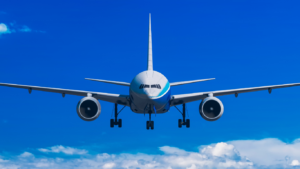
Think of a private jet and you might imagine celebrities, millionaires and high-flying business… Read more »
Think of a private jet and you might imagine celebrities, millionaires and high-flying business… Read more »
Porto Itapoá in Brazil avoided the consumption of over 1.18 million litres of fuel… Read more »
Bobcat will be presenting two major new developments at LogiMAT 2025 as part of… Read more »
AR Racking, storage solutions supplier, has successfully completed the implementation of its advanced AR… Read more »
Joloda Hydraroll Ltd, material handling expert and global loading and unloading solutions specialist, has… Read more »
Blue Giant Equipment Corporation, a leader in the development, manufacturing, and distribution of loading… Read more »
Following a busy Christmas period, work equipment owners are being advised to examine their… Read more »
Coinciding with COP26 in Glasgow, Hutchison Ports Port of Felixstowe has announced a major… Read more »
FedEx Express Europe has become the newest member of the Capital Equipment Coalition (CEC)… Read more »
Briggs Equipment has acquired JB Plant Hire, a Northern Ireland-based plant hire company. This… Read more »
According to a Eurostat study 10% of major injuries across European industry occur with… Read more »
Employee-owned packaging company, Kite Packaging, has recently expanded two of its popular pack room… Read more »
Briggs Equipment has announced it has completed the acquisition of Gwynedd Forklifts, an independent… Read more »
Easily manage inspection records and communicate equipment safety status where it matters most. Discover… Read more »
With the new Pallet Truck Tag and Powered Pallet Truck Tag, Brady Corporation claims… Read more »
Camso’s Solideal AIR 561 ground support equipment tyre is to equip TLD’s new driverless… Read more »
From palletisation to packaging, picking to production lines, Industry 4.0 has arrived and the… Read more »
Two Sany 4540 intermodal reach stackers have entered service at the ABP Hams Hall… Read more »
Manchester-based logistics equipment provider, Palletower, has announced it is to open its first European… Read more »
Employee-owned packaging company, Kite Packaging, are specialists in a cross-section of industries and their… Read more »
Advanced Handling, a UK specialist manufacturer of bespoke manual handling solutions, is to move… Read more »
Many an industrial truck operator considers switching from lead-acid batteries to lithium-ion technology when… Read more »
Lichfield-based logistics firm, Palletways 51, has invested more than £1.5million into its facilities and… Read more »
EnerSys®, the global leader in stored energy solutions for industrial applications, recently announced that… Read more »
Two UK companies have joined forces to help businesses whose employees are required to… Read more »
Qatar Airways Cargo has transported over 80 tonnes of oil and energy equipment on… Read more »
Briggs Equipment will be discussing its unique asset management proposition for port and freight… Read more »
A manufacturer of materials handling equipment has secured a £1 million finance package from… Read more »
GPS tracking data has been used to prove that a UK sandwich maker, Authentic… Read more »