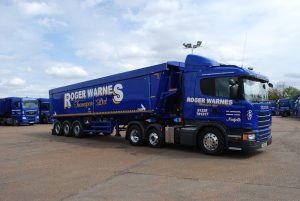
European regulators have been alarmed by the disproportionate share of CO2 trucks generate despite the fact they make up only 5% of the total traffic on European roads. CO2 emissions have continued to rise since the 1990s due to increasing road freight traffic and this issue is currently being discussed by EU leaders, who are focusing on measuring and reporting fuel consumption as a first step to cap CO2 emissions from heavy-duty vehicles,to see more please click here.
Cronus Logistics, one of the most innovative supply chain companies on the Irish-UK gateway understands the importance of reducing the amount of time spent travelling on UK and Irish roads and they are ahead of the curve in establishing their linehaul services.
Cronus Logistics has created an innovative service built on realising the importance of reducing road miles, driver hours, costs and cutting CO2 emissions. Pressure to lower emissions is mounting on manufacturers. There is currently no official method to measuring CO2 emissions from heavy-duty vehicles. As a step towards enforcing regulations the European Commission is introducing a Vehicle Energy Consumption Calculation Tool (VECTO) – a computer simulation measurement system that is expected to become mandatory as of this summer.
This is meant to be the first step in regulating emissions, however there are already concerns that VECTO won’t be effective due to the fact that there are so many different trucks on the market, making the industry too complex to be measured in this way. Rather than enforcing legislation that may not work in practice, by actually reducing the amount of time travelling on roads Cronus Logistics has tackled the problem head on.
Cronus Logistics is the only Irish Sea logistics company offering a comprehensive door-to-door service for dry freight, with full control of every element of the supply chain. This culminates in a reliable, competitive and green route to market.
Cronus has recently increased their services based on this ethos utilising two dedicated gateways – Bristol to Warrenpoint and Cardiff to Dublin. By linking these four ports they can strengthen the offerings to core manufacturing sectors to offer reduced road miles, lower CO2 emissions and tailored deliveries to customer requirements, alongside maintaining an industry standard 48 hour service.
If you want a service that demonstrates green credentials and saves on costs, Cronus is the logistics solution that reduces road miles, cuts CO2 emissions and contributes to a stronger financial bottom line.
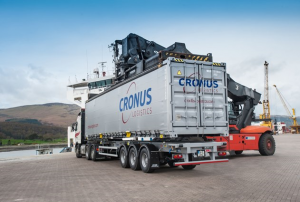
Cronus Logistics, one of the most innovative supply chain companies on the Irish-UK gateway understands the importance of reducing the amount of time spent travelling on UK and Irish roads and they are ahead of the curve in establishing their linehaul services.
Cronus Logistics has created an innovative service built on realising the importance of reducing road miles, driver hours, costs and cutting CO2 emissions. Pressure to lower emissions is mounting on manufacturers. There is currently no official method to measuring CO2 emissions from heavy-duty vehicles. As a step towards enforcing regulations the European Commission is introducing a Vehicle Energy Consumption Calculation Tool (VECTO) – a computer simulation measurement system that is expected to become mandatory as of this summer.
This is meant to be the first step in regulating emissions, however there are already concerns that VECTO won’t be effective due to the fact that there are so many different trucks on the market, making the industry too complex to be measured in this way. Rather than enforcing legislation that may not work in practice, by actually reducing the amount of time travelling on roads Cronus Logistics has tackled the problem head on.
Cronus Logistics is the only Irish Sea logistics company offering a comprehensive door-to-door service for dry freight, with full control of every element of the supply chain. This culminates in a reliable, competitive and green route to market.
Cronus has recently increased their services based on this ethos utilising two dedicated gateways – Bristol to Warrenpoint and Cardiff to Dublin. By linking these four ports they can strengthen the offerings to core manufacturing sectors to offer reduced road miles, lower CO2 emissions and tailored deliveries to customer requirements, alongside maintaining an industry standard 48 hour service.
If you want a service that demonstrates green credentials and saves on costs, Cronus is the logistics solution that reduces road miles, cuts CO2 emissions and contributes to a stronger financial bottom line."/>
Teesport To Handle Hitachi Rail Car Imports

North-east England based PD Ports will handle the majority of Hitachi Transport System Europes… Read more »
French Robots-in-Ports Plan Receives Funding Boost
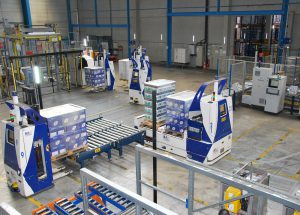
Driven by GAUSSIN SA and BA Systèmes, VASCO is a collaborative project of innovation… Read more »
Bowl a winner with Sports Logistics
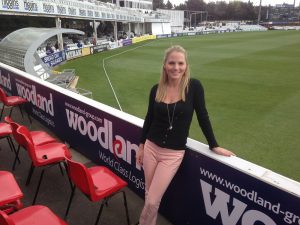
Global freight forwarder Woodland Group has padded up and is ready to bowl a… Read more »
Kerry Logistics Wins Concession To Operate Inland Ports In Myanmar To Strengthen Footprints In The Greater Mekong Region

Kerry Logistics Network Limited (Kerry Logistics or the Company; Stock Code 636.HK), a leading… Read more »
Quality Freight and Peel Ports launch new container service

Logistics and shipping specialist Quality Freight UK and Peel Ports have launched a new… Read more »
PD Ports Celebrates First Anniversary Of Teesport Rail Terminal

Today marks the first anniversary of PD Ports intermodal rail terminal at Teesport. PD… Read more »
LNG shipping under pressure from tumbling European re-exports
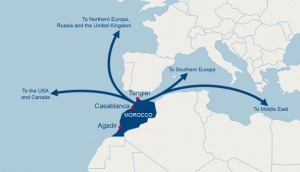
LNG shipping freight rates continue to be under pressure from weak Asian demand and… Read more »
Menlo Supports Academic Achievement in Supply Chain Management

Menlo Logistics (Menlo), the global logistics subsidiary of Con-way Inc. (NYSE: CNW), is continuing… Read more »
Hutchison Ports Thailand Achieves Container Handling Milestone

Hutchison Ports Thailand (HPT) held an event on Wednesday (21 October) to mark the… Read more »
Yusen Logistics UK Supports First National Lorry Week

Yusen Logistics UK is supporting National Lorry Week, a new initiative led by the… Read more »
PD Ports Sees JDR Expand Service Footprint At Port Of Hartlepool, UK
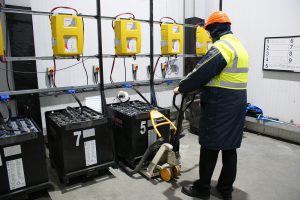
JDR, a leading provider of technology connecting the global offshore energy industry, has expanded… Read more »
Peel Ports Introduces Virtual Crane Operations At Port Of Liverpool
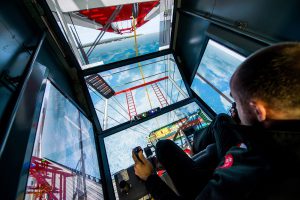
In anticipation of the arrival of five of the worlds largest cranes at the… Read more »
New Greenock service to connect Scottish exports to deep-water ports in Liverpool and Rotterdam via Belfast
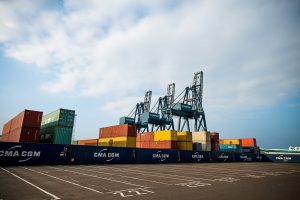
A new shipping service from Greenock to Rotterdam via Liverpool and Belfast will open… Read more »
GEFCO reports positive results in Algeria just one year after setting up its local subsidiary
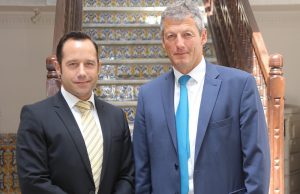
The GEFCO Group, European leader in Automotive logistics and a global benchmark in industrial… Read more »
Swisslog Realises Click&Pick Solution at LIDS Sports Groups Central Distribution center

LIDS Sports Group has launched its newly installed goods-to-person solution, utilizing Swisslogs award-winning AutoStore… Read more »
YCH supports ZALORA to launch the biggest fashion warehouse in Indonesia
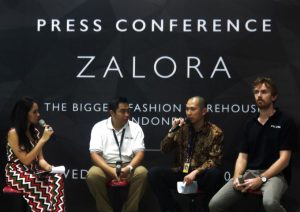
YCH Group, Asia Pacific’s leading integrated end-to-end supply chain management and logistics partner, implements… Read more »
PEEL PORTS LAUNCHES CARGO200 INITIATIVE
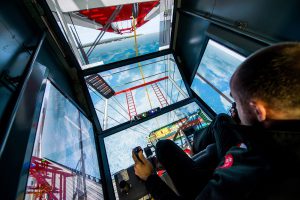
The UKs second largest ports operator, Peel Ports, has today (Wednesday, 29 April) launched… Read more »
GCS Group handles growing volumes of Russian project cargo exports

Transcontainer LLC and RUSCON, two divisions of the GCS Group, are among the many… Read more »
Interroll reports strong order income and high sales growth in 2014

The Interroll Group managed to successfully continue on its growth course in financial year… Read more »
TT Club Warns Baltic Ports to Protect Against Reputational Damage
Speaking during Baltic Transport Week in Gdansk this week Andrew Huxley, Development Director at… Read more »
Jungheinrich reports record results: Net sales grow by 9%

Net sales grow by 9 per cent to 2.5 billion euros Incoming orders over… Read more »
Ruslan International transports stripping tower to Kurdish oil field in first of its kind operation
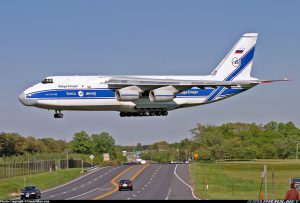
Ruslan International demonstrated its unfailing capability in heavy and outsize air cargo last month,… Read more »
MPI OFFSHORE SIGNS SIX YEAR DEAL WITH PD PORTS
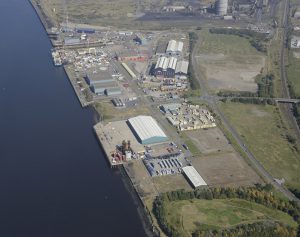
MPI Offshore has signed a six year lease agreement with PD Ports to secure… Read more »
MPI OFFSHORE SIGNS SIX YEAR DEAL WITH PD PORTS
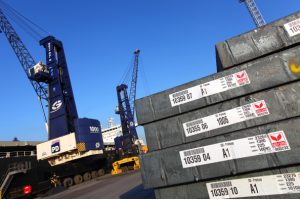
MPI Offshore has signed a six year lease agreement with PD Ports to secure… Read more »
Swisslog reports high order intake and order backlog

According to the preliminary figures, Swisslog stepped up its order intake and net sales… Read more »
Dematic Completes Commissioning of AutoStore Project

Dematic has recently finalised the delivery and installation of an AutoStore system for Righi… Read more »
Thames Light Freight Project Looking for Partners
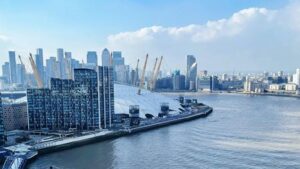
The Thames Estuary Growth Board (The Growth Board) is seeking partners to join a… Read more »
Reducing Pollutant Emissions in Shipping

Reducing pollutant emissions in the shipping industry can be achieved by using clean, alternative… Read more »
Megacentre for Spices and Herbs Opens

From anise to cinnamon, Greiwing logistics for you GmbH is extending its service portfolio… Read more »
Beat the Clock for Time Critical Cargo

The Antonov 124, one of the largest commercial aircrafts in the world, was recently… Read more »
Compact and Scalable Sorting System

At the end of last year, Collo-X, an innovative company based in the Netherlands,… Read more »