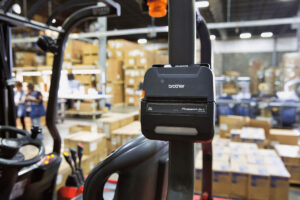
Business technology solutions provider Brother UK has launched a new labelling self-assessment tool designed… Read more »
Business technology solutions provider Brother UK has launched a new labelling self-assessment tool designed… Read more »
Transport SMEs are ready to ramp-up investment, with fresh spending on assets and expanded… Read more »
Big Box Automation, part of Big Box Group, has added Radio Frequency Identification (RFID)… Read more »
Transmetrics, a state-of-the-art AI platform developed exclusively for the supply chain, has announced that… Read more »
Transmetrics, a frontrunner in predictive optimisation for the logistics industry, has opened an office… Read more »
Automation used to be about the multi-billion turnover, blue-chip global players putting out global… Read more »
Low-CapEx technology is leading SMEs to look at flexible and scalable, warehouse automation as… Read more »
Freshways is the UK’s largest independent processing dairy and provides wholesalers, manufacturers and other… Read more »
One of the UK’s many SME importers, Active Products (UK) Ltd, has successfully become… Read more »
Appliance manufacturer Smeg UK has awarded Yusen Logistics UK the nationwide retail and trade… Read more »
Small and medium-size businesses that have struggled for equal footing in the global economy… Read more »
Agility has launched the first fully integrated online freight service, allowing users to get… Read more »
Supply chain optimiser Quintiq is to partner with Alro, the largest aluminium smelter in… Read more »
Reply, through the two companies Storm Reply, Amazon Web Services Premier Consulting Partner, and… Read more »
More than one in three (39%) small to medium transport businesses have turned down… Read more »
More than 63% of British small and medium sized enterprises (SMEs) are exporting and… Read more »
SMEs are making a positive contribution to narrowing the UK trade deficit, according to… Read more »
Brexit’s second chapter shows that UK-EU Supply Chains have survived, but adapted. Logistics must… Read more »
Year Two of Bobcat’s ownership of the former Doosan forklift brand, and we’re starting… Read more »
Rugged devices and mobile computers can improve supply chain performance for transport operations, field… Read more »
What exactly does Extended Producer Responsibility entail, and how should logistics businesses respond? Carrie… Read more »
At the Last Mile Leaders Europe event last week FarEye revealed its latest industry… Read more »
Evri, one of the UK’s largest dedicated parcel delivery companies, and DHL eCommerce, the… Read more »
Industry mergers continue apace, including in the reusable plastic packaging sector. They may provide… Read more »
transport logistic 2025 (TL Munich) will take place from June 2 to 5th at… Read more »
Clustag RFID Solutions has opened a new Experience Centre for its customers in Miami… Read more »
Circet, a European provider of telecommunications infrastructure services, has improved safety, reduced emissions and… Read more »
The historical trade route that connected the civilizations of China and Europe is undergoing… Read more »
Property investors and owners are facing a fundamental shift in how they understand and… Read more »
Today’s forklift industry experiences both as many changes as challenges. Over the last year… Read more »
 Hitachi ZeroCarbon today unveils a holistic suite of EV fleet solutions designed to simplify every… Read more »
Libiao Robotics, a supplier of warehouse robotics automation solutions, has been awarded a 2025… Read more »
In today’s fast-paced industrial landscape, ensuring workplace safety is paramount. Beyond the immediate human… Read more »
Freedom to integrate best-of-breed technology delivers the flexibility, scalability and fast ROI businesses crave.… Read more »
Samsara Inc. today announced the launch of its Electronic Brake Performance Monitoring System (EBPMS)… Read more »
The recent closure of Heathrow Airport has sparked renewed urgency around resilience and supply… Read more »
Professionals from across the logistics and supply chain sector spoke about challenges and opportunities… Read more »
Dexory aims to help its customers enter a new era of warehouse intelligence with… Read more »
Europe is facing a severe truck driver shortage – around 230,000 driver roles remain… Read more »
The leaders of physical operations-led organisations in the UK and Ireland reveal how putting… Read more »
DHL Global Forwarding, the ocean and air freight division of DHL Group, has published… Read more »
The logistics industry is evolving at an unprecedented pace, with growing warehouse management demands… Read more »
As part of a company-wide digital transformation to overcome labour shortages, a leading Japanese… Read more »
Girteka is shifting toward more sustainable operations by combining rail and road transport and… Read more »
IFCO, a supplier of reusable packaging solutions for fresh food, achieved record environmental savings… Read more »
LogiMAT 2025 will be the stage for innovations – experience how SSI Schaefer is… Read more »
LogiMAT 2025 is once again filling over 120,000 square metres in all ten exhibit… Read more »