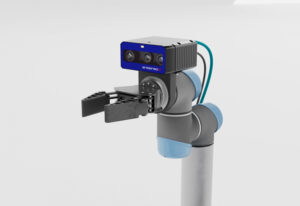
IDS Imaging Development Systems introduces a new 3D camera in the Ensenso product line.… Read more »
IDS Imaging Development Systems introduces a new 3D camera in the Ensenso product line.… Read more »
Webfleet, Bridgestone’s global fleet management solution, has launched the EV Transition Tool to support… Read more »
INFORM announces the opening of a new office in Portugal. With this step, the… Read more »
INFORM, a global software provider for AI-driven Digital Decision-Making optimizing business operations, headquartered in… Read more »
KLM Royal Dutch Airlines has opted for AI-powered WorkforcePlus software to optimise workforce scheduling… Read more »
INFORM, a leading provider of AI-based optimisation software that facilitates improved decision making, processes… Read more »
Within just two weeks, Aachen-based optimisation specialist INFORM implemented its Vehicle Yard Management System… Read more »
INFORM, a leading provider of AI-based optimisation software that facilitates improved decision making, processes… Read more »
The Information Factory, an independent software vendor specialising in the logistics sector, has launched… Read more »
WEBINAR: Algorithms are a proven way to optimise pooling operations, as they provide the… Read more »
Inform has successfully integrated Linker, a proven middleware, into ITS Synrotess Rail Scheduler, an… Read more »
Piraeus Port Authority (PPA) S.A., member of COSCO SHIPPING Group, has decided to invest… Read more »
A customised IT solution in vehicle logistics from software provider INFORM for ASB Logistics… Read more »
INFORM has successfully deployed its Syncrosupply Time Slot and Yard Management system to logistics… Read more »
Logistics software vendor The Information Factory has appointed three software developers; Tomas Rohr, Mihai… Read more »
One of the UK’s most important and respected retailers, John Lewis & Partners, has… Read more »
Storopack is a specialist in the field of protective packaging. Its product portfolio encompasses… Read more »
In the modern age of logistics, the warehouse is no longer a static storage… Read more »
Manhattan Associates Inc., a global leader in supply chain commerce, has announced the findings… Read more »
The new facility harnesses renewable energy and sustainable solutions, achieving BREEAM ‘Excellent’ and LEED… Read more »
How is the maritime sector navigating the twin pressures of decarbonisation and digitalisation? What… Read more »
The British International Freight Association (BIFA) is strengthening its sponsorship and collaboration with the… Read more »
Delivering results is the reason why logistics and shipping support teams are adopting agentic… Read more »
Samsara has just launched more than a dozen new safety and AI-powered tools designed… Read more »
Whether conveying goods or lifting heavy loads, every movement needs a drive system. However,… Read more »
The benefits of e-documentation in logistics are improved collaboration, operational efficiency and substantial reduction… Read more »
The new ultra-compact RSL 200 safety laser scanner from Leuze can be integrated effortlessly… Read more »
The logistics industry is undergoing rapid change, with 87% of logistics operators planning to… Read more »
BRA Isogona, a leading manufacturer and marketer of cookware and tableware, has shown consistent… Read more »
DP World has unveiled a fully integrated logistics and market-entry solution aimed at addressing… Read more »
Customs Support Group (CSG), provider of customs clearance and trade solutions, is introducing a… Read more »
Transparency of the global supply chain is becoming the weapon of choice for smart… Read more »
In response to today’s high demand for resilience in the world of physical operations,… Read more »
Bold new branding for end-to-end system integration specialists TGW Logistics represents confidence, flexibility and… Read more »
Logistics Business magazine, together with the Information Factory, have produced a new 8 page… Read more »
Rugged devices and mobile computers can improve supply chain performance for transport operations, field… Read more »
What exactly does Extended Producer Responsibility entail, and how should logistics businesses respond? Carrie… Read more »
Körber Supply Chain Software, a joint venture between Körber AG and KKR recently introduced… Read more »
Experience and track record matter in freight forwarding, according to Paul Everley, Global Head… Read more »
Logistics companies face immense pressure to optimise their operations, enhance security, reduce losses, and… Read more »
Automated picking and handling operations often require the usage of more than one technology… Read more »
While the main focus is on tariffs, trade lanes – as arteries of the… Read more »
Risk mitigation is imperative to reduce the risks of and damage from cyberattacks and… Read more »
Everyone in our industry knows what Third-party contract logistics is (3PLs and LSPs). Many… Read more »
Visitor registration is now open for the International Materials Handling Exhibition (IMHX) 2025, the… Read more »