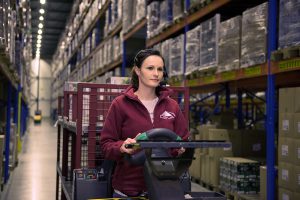
How to manage peak season – a personal view from IBM Systems Architecture team:… Read more »
How to manage peak season – a personal view from IBM Systems Architecture team:… Read more »
There is personnel change on the Management Board at Hamburg-based forklift truck and warehouse… Read more »
Founded and headquartered on the remote Isle of Islay in the Inner Hebrides in… Read more »
The first shipment of pallets has arrived at the new Isle of Harris Distillery… Read more »
Realogis Germanys leading consulting firm for logistics properties, industrial properties, and commercial parks… Read more »
These words were spoken by Steve Goodall, operations manager at the Budgens distribution centre… Read more »
Transport and logistics is a highly regulated industry when it comes to health and… Read more »
Reducing pollutant emissions in the shipping industry can be achieved by using clean, alternative… Read more »
AR Racking, storage solutions supplier, has successfully completed the implementation of its advanced AR… Read more »
Supply chain visibility is the nirvana for most supply chain and logistics managers. It… Read more »
Ian Cairns (pictured), Sales Director at TalkTalk Business discusses why a resilient network is… Read more »
By 2050, Europe should be the first CO2-neutral continent – that is the goal… Read more »
Every industry, from retail to construction, relies on its supply chain for processes and… Read more »
The aim of the partnership between EPG’S Greenplan and customer Anaxco is to combine… Read more »
STILL, the Hamburg-based intralogistics provider, is systematically expanding its service concept and will soon… Read more »
Today’s main challenge in the logistics and transport sectors is decarbonisation. Electric trucks, intermodal… Read more »
Once enforcement of the new AI act begins, organisations may face fines as large… Read more »
The collapse of the Baltimore bridge is a tragedy. But the impact on supply… Read more »
Stoecklin Logistics, a leading provider of automated material handling and warehouse storage systems, announced… Read more »
Online to inflight, ecommerce is transforming international express courier services, writes Matthew Ware, CEO… Read more »
We can observe that all small or large scale businesses are in a serious… Read more »
SICK has unveiled a pioneering compressed air monitoring system that accurately predicts where significant… Read more »
DHL and New York University’s Stern School of Business today released the new DHL… Read more »
Ancra Systems is a leading specialist automatic truck, trailer, and container loading and unloading… Read more »
ABM will present complete drive solutions for a wide range of intralogistics applications at… Read more »
Red Bull’s Formula One HQ in Milton Keynes is an appropriate and impressive backdrop… Read more »
Finding ways to deliver more while keeping costs low is a driving force in… Read more »
Stansted Airport in Essex is FedEx’s biggest cargo hub in Britain. David Priestman grabbed… Read more »
Businesses across all sectors are looking to AI, whether it’s to improve productivity and… Read more »
The automation of hand scanning processes increases productivity at inbound and outbound areas of… Read more »
Logistics Business magazine, in association with Sentry Protection Products, have produced a new digital issue… Read more »
At the upcoming LogiMAT in Stuttgart, March 19th to 21st, Dematic highlights how every… Read more »
In December 2023, ABB Electrification Norway AS signed a contract with LIS, Movu Robotics’… Read more »
New research by Capgemini reveals that the eco-digital economy is expected to double in… Read more »
Specialist 3PL fulfilment provider Europa Warehouse has reported a 45 per cent increase in… Read more »
Exhibitors from nearly every sector of the industry are coming to LogiMAT 2024 to… Read more »
Port Boulogne Calais has once again demonstrated its resilience both in terms of fishing… Read more »
The IFOY organization has announced the nominations for the IFOY AWARD 2024 and once… Read more »
When the Samworth Brothers company was looking for a new hanging sign for its… Read more »