Unrivaled Performance of Li-Ion AGV Batteries
22nd February 2024
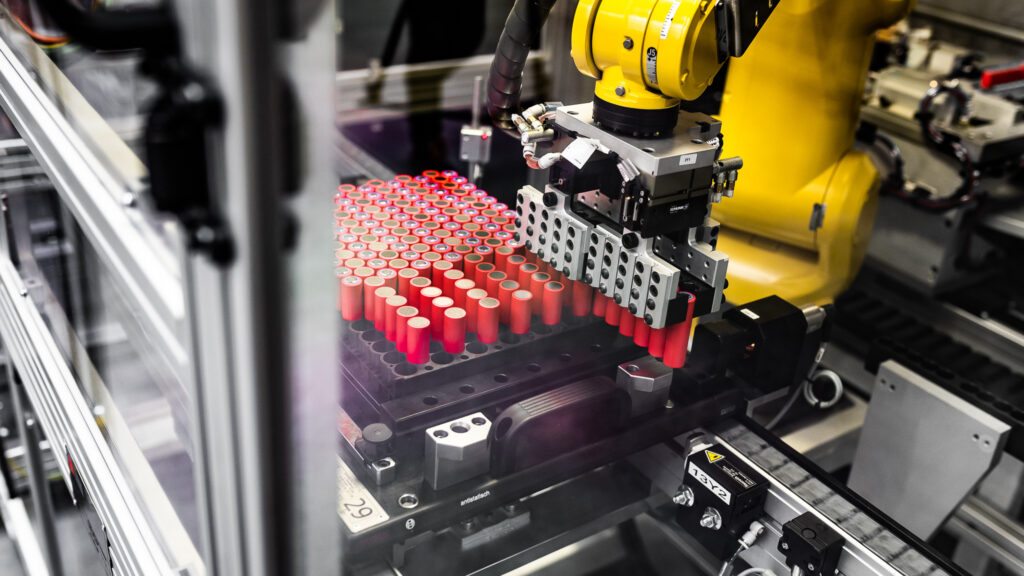
Finding ways to deliver more while keeping costs low is a driving force in the logistics industry, and many providers are turning to technology to find better solutions, according to Johnson Matthey Battery Systems.
Advances in Lithium Ion (Li-ion) batteries have seen them leapfrog traditional lead-acid batteries, providing safer, better value power for autonomous options like Automated Guided Vehicles (AGVs) and Autonomous Mobile Robots (AMRs). This article looks at how lead-acid and Li-ion batteries compare from a technical perspective, as well as how they stack up when it comes to safety and cost.
Energy density
Li-ion batteries are known for their energy density. Crucial for a logistics environment where space and weight are at a premium, Li-ion batteries now comfortably offer 160-190 Wh/kg, even under 100% Depth of Discharge (DoD). That’s five times more energy dense as lead-acid options (30-50 Wh/kg). High energy density options, such as NCA and NCM cells, can even reach a staggering 270+ Wh/kg — enough to power an electric bike for roughly 80-120 km on a single charge.
Number of cycles
Li-ion batteries also outperform lead-acid options when it comes to lifespan by a factor of four. Lead-acid batteries typically only last 500 cycles, fewer if you’re running the battery all the way down; Li-ion phosphate batteries can pass the 2,000 cycle mark and perform especially well under demanding deep discharge conditions.
Charging times & requirements
With a maximum current limit of 0.3C, lead-acid batteries take longer to charge and require dedicated charging areas with hydrogen monitoring. Li-ion batteries, however, can take a higher charging current of 1C or more, enabling them to recharge much quicker — a clear advantage in an industry that wants to limit downtime.
The perceived risk
Despite outperforming lead-acid batteries from a technical perspective, some prospective buyers still have concerns around the fire risk. Challenges such as overheating, overcharging, or mechanical damage to Li-ion cells can potentially trigger thermal runaway, posing a fire risk. To minimize this risk, high-quality Li-ion batteries incorporate a Battery Management System (BMS). These systems monitor crucial parameters like temperature, current, and voltage, quickly deactivating the battery in the event of a breach. In comparison, lead-acid batteries lack BMS and rely solely on the charger for protection.
Li-ion batteries have continued to develop, and the inclusion of iron phosphate to create LFP batteries is a big step forward when it comes to safety. Using iron phosphate as the cathode material makes the battery more stable, gives a longer cycle life and increases the tolerance to high temperatures and abuse, significantly reducing the fire risk and increasing battery safety.
Upfront costs
There’s a perception that Li-ion batteries are expensive, and higher upfront costs are often the biggest factor that puts people off using them. While there is a higher initial investment, to truly calculate the cost of a battery you need to factor in its lifespan, reliability, uptime, and maintenance requirements.
Lifespan
The total cost of ownership over a battery’s lifespan makes Li-ion the smarter financial choice. Li-ion batteries don’t need to be replaced as frequently as older lead-acid batteries. Their ability to cope with deep discharge cycles, even up to 100% in the case of LFP variants, significantly extends their operational life.
Data-Driven replacement
In heavy usage environments, the last thing you want is to suddenly find yourself without power. Being able to integrate BMS into Li-ion batteries allows you to make timely, cost-efficient decisions about how long a battery will last and when to replace it. Ultimately, Automated Guided Vehicles are all about boosting productivity and profitability, and one of the biggest drains on productivity is downtime.
Li-ion batteries can handle a higher charging current of 1C or more, allowing them to charge at a much faster rate compared to other battery types. Quicker charging reduces the downtime of the AGV; vehicles spend less time in the warehouse or factory waiting for batteries to recharge and more time out on the road.
Maintenance
Lastly, one of the costs people often overlook when comparing lead-acid and Li-ion batteries is the ongoing maintenance. Keeping lead-acid batteries performing at their best requires frequent maintenance, such as cleaning to control corrosion and ensuring terminals are tightly connected. Li-ion batteries, however, are maintenance free.
When it comes to the next generation of AGV-powered logistics, Lithium-Ion (Li-ion) batteries outshine lead-acid options on every front. Their energy density, higher number of cycles, and the ability to add Battery Management Systems make them the clear winner when it comes to technology and safety. And they’re also the smarter choice budget wise: safer batteries that last longer, recharge quicker, and don’t require ongoing maintenance make Li-ion batteries a cost-efficient, reliable solution for future-focused logistics operations. To get the full safety and reliability benefits of Li-ion batteries, make sure you’re partnering with a reputable supplier who can source high-quality batteries based on your needs and timelines.
Read more: