Stretch Wrapping is Ecological and Cost-effective
23rd March 2022
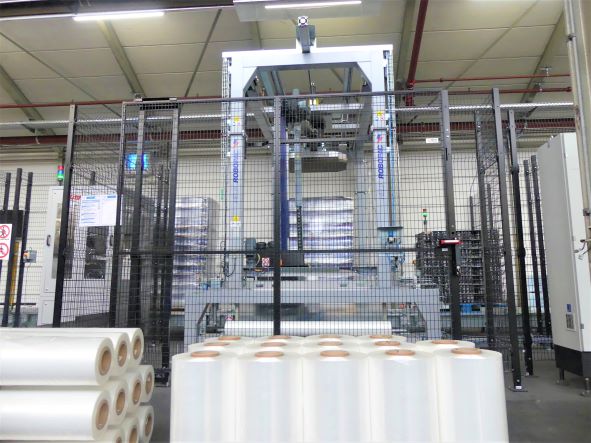
Life cycle management, sustainability and environmental friendliness are terms that are now firmly anchored not only in the minds of end consumers, but also in the minds of more and more companies. However, the consistent implementation of such measures should also have as positive an effect as possible on costs.
Robopac Germany, a company of the international Aetnagroup, focuses on intelligent packaging machines for stretch wrapping technologies in the food and beverage industry, which are tested and permanently updated in its own TechLabs. Premium versions include, for example, a new generation of high-performance ring wrapping machines with patented Cube Technology, suitable for wrapping and stabilising pallets with stretch film.
For many packaging companies, it is a technical challenge to always wrap pallets with a wide variety of goods stably and with as little film as possible. Each load is different in height, width, weight and is made of a different material. For example, pallets with canned goods have to be wrapped differently than beverage crates, bottles or milk cartons. Often, several layers of film are packed in the lower part of the pallet to make it seemingly more stable for transport. In fact, it’s the other way around.
The load often fluctuates the most at the top and would need more support here through a larger film volume. This is exactly where Robopac comes in with its mix of technical, physical and scientific know-how. At the customer’s site, if requested, a service technician will check the pallets to be wrapped – prior to wrapping them with stretch film. They then individually set the appropriate program on the machine to ensure optimum wrapping. With the help of Cube Technology , exactly the right amount of film is applied at exactly the right place with exactly the right pre-stretch. The pre-stretch ensures the correct containment force of the load and thus maximum stability.
Another positive side effect of the patented wrapping technology is that in some cases up to 70 percent of film material can be saved in this way without sacrificing the highest possible quality. However, not every stretch film is equally suitable for use in these high-performance packaging machines. The film material must, for example, run at high wrapping speeds and have strong flexibility and load stability, such as films from manupackaging.
Converted to the daily goods throughput of an average brewery of 1,400 pallets, around 280kg less plastic can be used here. Multiplied by an annual production, the savings amount to up to 70,000kg of plastic or the equivalent of €140,000.
On the cost side, companies can expect some massive changes in the near future. Since January 1st, 2021, the federal government still pays €0.80 to the EU for every unrecycled kilogram of plastic. However, there are plans to distribute these not inconsiderable expenses among companies in the future. In other words, this means a correspondingly high financial burden for companies with a high plastic consumption. Prices of up to €2 per kilogram are currently being discussed. On the other hand, companies that consistently recycle or already use intelligent wrapping technology in their packaging will have a permanent advantage.
similar news