SNCB Logistics improves profitability, efficiency and productivity with Quintiq
20th January 2015
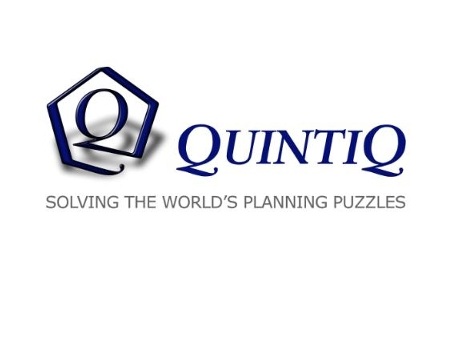
As you know, the rail freight industry has historically been losing money. To be competitive and profitable, SNCB Logistics needed to look at restructuring itself completely. SNCB Logistics is an independent freight rail operator within the Belgian rail group SNCB. Headquartered in Brussels, it is active in Western Europe. The company handles rail freight production in Belgium and its surrounding countries.
SNCB Logistics’ rail cargo-planning challenge was highly complex. For the long- and short-term planning of all its locomotives, drivers, local station staff and rail paths, the company had to take into account constraints such as maintenance rules, route and traction knowledge. Different working time directives and regulations for the various personnel types also had to be factored in. What made planning even more complicated was the fact that the companys planners had, for historical reasons, been using separate planning systems for locomotives, train drivers, station staff and rail paths.
To control its entire production chain, SNCB Logistics wanted to replace these systems with a single, integrated solution that would offer company-wide transparency. It wanted a solution that would enable total resource planning: from station staff and train drivers to locomotives and rail paths, and across all planning horizons, from long term to day of execution.
Initially, SNCB Logistics published a tender. Based on criteria such as speed of the systems deployment, user friendliness and return on investment, the companys managers opted for the collaborative solution proposed jointly by Quintiq and Ab Ovo, Quintiqs implementation partner.
SNCB Logistics was going through profound restructuring and was aiming for significant improvement in quality and productivity. We had already achieved significant results in these areas, but to have more impact, we needed an integrated IT system that would allow us to perfectly synchronize planning of all processes as well as our resource utilization. Moreover, this system had to be integrated and implemented very quickly, says Geert Pauwels CEO, SNCB Logistics.
Pauwels, CEO of SNCB Logistics. After an intensive selection process, we decided to choose Ab Ovo and Quintiq. The proven, state-of-the-art Quintiq software in combination with Ab Ovos specific rail planning and scheduling expertise perfectly matched our business requirements.
Today, SNCB Logistics’ planning system has about 150 primary users and 60 auxiliary users. Soon, this will grow to 200 primary users and 100 auxiliary users. The implementation of an integrated planning system allows the firms managers to plan based on actual demand and get a precise and transparent view of required resources.
If you would like some further information on this implementation, please let us know. We can also organise an interview with Quintiq if you would prefer.