Case Study: UniCarriers Provides Total Solution For UK Food 3PL
6th July 2017
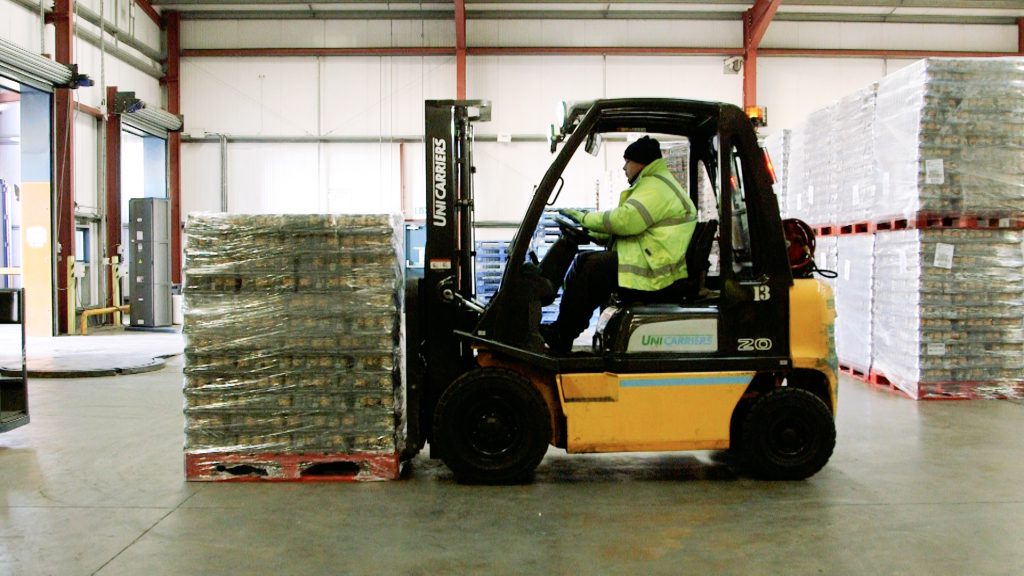
As a service provider for food logistics, some of the biggest retailers of the United Kingdom are among Boughey Distribution’s customers. In order to meet their tightly scheduled delivery dates and ensure fast turnover of goods, the company relies on forklift-managed logistics at its warehouse location in Nantwich. As the sole machine supplier, UniCarriers provides a fleet of 100 counterbalance trucks and warehouse trucks in total for this purpose, which handles all the tasks of the internal company material flows. To maximise the vehicles availability, two UniCarriers technicians provide reliable all-round service on site, five days a week.
The capacities of the logistics service provider Boughey Distribution at its location in Nantwich, Cheshire, are impressive: there are a total of 100,000 pallet places available here, distributed across 15 warehouses. As a result, the company is one of the leading service providers, for the storage and distribution of food in the United Kingdom. Apart from stockholding and punctual delivery of goods to supermarkets, Boughey also provides value-added services, such as copackaging. All goods movements on the 85,000 m2 logistics site are made with forklifts. “For our business model, it’s essential we guarantee the customer punctual delivery at any time,” explained Dave Vernon, Warehouse Manager at Boughey Distribution. “That’s why we depend on a sturdy, absolutely reliable forklift fleet. UniCarriers’ fleet fits the bill ideally.”
Joint growth
The partnership between Boughey and UniCarriers extends to over 30 years and has been successively expanded. In the past, Boughey sourced its warehouse trucks exclusively from the original UniCarriers brand Atlet. “As UniCarriers offer a full range of forklifts, we thoroughly examined their overall capability, and decided in 2016 to use the company as the sole machine supplier,” revealed Dave Vernon. Consequently, the 100 UniCarriers rented forklifts that help to meet Boughey’s tight delivery deadlines, have recently also included 37 counterbalance trucks. The size of the fleet is a result of the constantly growing storage capacities: Boughey has continuously expanded its logistics site at Nantwich. The latest number 13, 14 and 15 warehouses alone hold 59,000 of the total 100,000 pallet places. UniCarriers also provided support in planning the facilities – with the Logistics Analyser, simulation software that is part of the comprehensive service package UniCarriers 360°. The software identified the ideal storage solution and the matching forklift fleet for Boughey on the basis of the logistical requirements and material flows. “UniCarriers in effect grew its range of products and services in-line with our requirements,” according to Dave Vernon. “That’s a major reason for our long and successful cooperation.”
Customised logistics solution
This is what the ideal solution at Boughey looks like: all products are stored on flexibly adjustable pallet shelves and mobile shelves that permit optimal use of space. The shelves are stocked using UHX and UMS reach trucks. These raise up to 1250 kg heavy pallets as high as 11.1 m to the shelf levels. Thanks to the tilting seat, which can be easily inclined by up to 18°, ergonomic posture of the head and neck muscles is maintained at all times. To keep an ongoing overview of all products stored in the 15 warehouses, Boughey relies on perpetual inventory of the stocks. This involves the logistics service provider permanently comparing the goods on hand with the data filed in the system and making corrections where needed. OPS high level order pickers are used to perform the inventory. If an article is required for shipment, the reach trucks retrieve the pallets needed and place them in the picking area. The customer orders are assembled using PLP low lift pallet trucks, which are also employed for loading and unloading trailers at the rear. By contrast, Boughey uses DX 20 and DX 32 gas-powered counterbalance trucks for side-loading of trailers and for internal transport of pallets on-site. The five models designed for simultaneous transport of two pallets permit especially fast despatching of trailers. Given 26 pallets per trailer, double pallet handling makes for significant time-savings.
Safety during all work stages
Among other things, the products stored by Boughey include aerosols, these containers are pressurised and could explode. This is why only specially-equipped reach trucks are used in warehouse areas with aerosols. They have a Gas Checka System that permanently tests the ambient air and warns warehouse staff upon the escape of explosive gas. Moreover, all reach trucks safety equipment includes a Stability Support System (S3). This permanently checks the driving characteristics of the forklifts and intervenes in the event of danger. For example, speed that is excessive when turning corners is automatically reduced to prevent the forklift tipping. “Our highest priority is the health and safety of our employees and UniCarriers equipment helps us to achieve this,” Dave Vernon was pleased to note. For example, the floating armrest and mini-steering wheel of the reach truck are unique. These permit effortless vehicle steering and contribute to avoiding employee illnesses due to repetitive strain injuries. UniCarriers has also developed an appropriate concept for changing the heavy forklift batteries: the Battsman, a vehicle with an electromagnetic installation that is docked onto the flat battery before removing it from the forklift and replacing it with a new one. This keeps manual handling to a minimum and as a result permits safe and ergonomic battery changing.
On-site technician support
To achieve maximum availability of the forklift fleet, two UniCarriers technicians are on the spot at Boughey five days a week – one specialist for counterbalance trucks and one for warehouse trucks. They operate their own spare parts warehouse in the logistics centre. “The reliable customer service decisively influenced our decision to use UniCarriers as the sole machine supplier,” said Dave Vernon. “We can fully concentrate on our core business while the technicians ensure optimal fleet operation.” But UniCarriers and Boughey’s cooperation is not just aimed at the preservation of the status quo through service inspections. Regular review meetings including personnel from both companies are the basis for a continuous improvement process. Among other things, this involves investigating potential for cost optimisation. This includes utilisation of the machines over their six-year rental period or reducing forklift damage. UniCarriers fleet management system VOM, which Boughey is in the process of testing on three forklifts, can help with the latter. The system permanently collects and evaluates usage data of vehicles. In this way the causes for damage to forklifts can be better recognised and corrected. If the test is successful, VOM is to be introduced across the whole fleet.