Nuremberg LogisticCity: Recycled Paper, not Plastic
27th June 2023
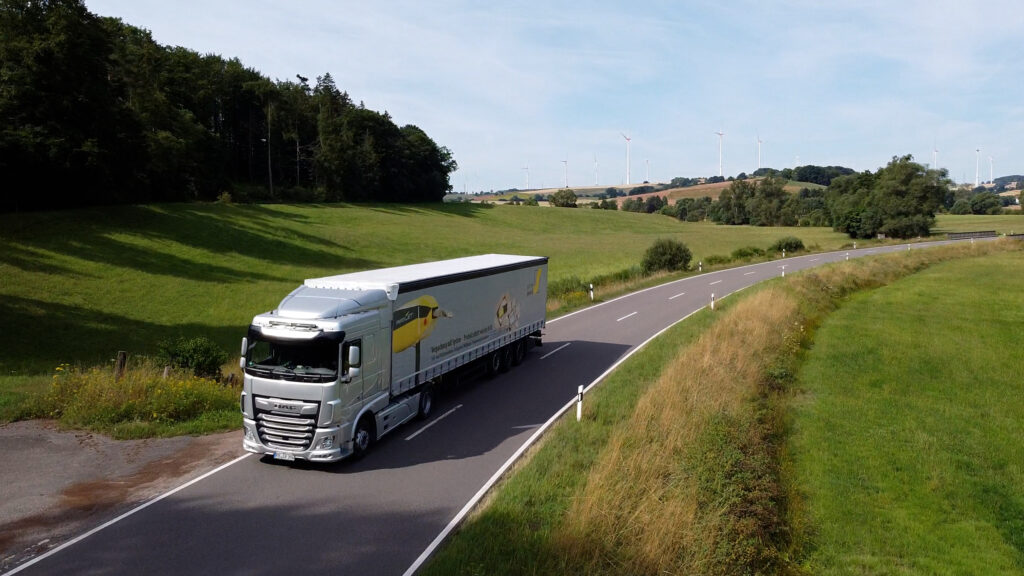
The LogisticCity in Nuremberg is the logistics centre of the Hoffmann Group, which was put into operation at the end of 2021. As a market-leading partner for quality tools, the company supplies over 135,000 customers worldwide. The increased output of the highly automated LogisticCity led to the evaluation in use of protective void fill cushioning materials. To meet the new requirements of the packaging process, Papier Sprick supplied the PaperJet cushioning system, a demand-oriented and efficient solution.
120,000 different catalogue items, 80 packing stations and up to 40,000 packages per day ‒ the LogisticCity presents complex demands on a packaging solution. Before the LogisticCity was built,
Hoffmann Group used foil cushions as padding material. Junior Project and Process Manager Jonas Karg remembers: “The topic of filling or cushioning material was a puzzle that had to be reassembled. From employees to upper management, everyone was involved in the project.”
Several impulses shifted the decision in the direction of recycled paper: The innovative idea behind the LogisticCity was to be carried forward in the area of sustainability. “The desire for a more eco-friendly packaging material was also expressed by customers,” says Karg. In addition, regulatory requirements for importing plastic foil to other countries influenced the decision-making process. At FACHPACK in September 2019, before the finalization of the LogisticCity, Hoffmann Group and Papier Sprick engaged in dialog for the first time.
The very next month, the first test setups were carried out at the established Nuremberg site, which were expanded into the building of LogisticCity in April 2020. Paper- and foil-based solutions from various manufacturers were put to the test in practice and evaluated by employees based on feedback sheets, among other criteria. Papier Sprick submitted the PaperJet, an extremely fast system for the production of paper cushions.
The test clearly highlighted the advantages of the PaperJet over the film solution and other paper-based materials. “Initial scepticism about the paper solution was quickly dispelled. The employees favoured the PaperJet and preferred to work at these stations,” says Michael Scholz, Team Leader Logistics Small Packaging.
Jörg Kaschny, Field Sales Manager of Papier Sprick’s, was on hand to advise from the start of the test phase. “This reliable service was very valuable for us,” says Karg. “With Mr. Kaschny, we have a single point of contact who takes care of all matters.” The test setups were accompanied by training sessions for packaging. Here, Kaschny informed the employees about cushioning and packing options, carton sizes and the workflow. Scholz emphasizes, “This gave our employees an understanding of the material and cushioning with paper.”
By integrating the PaperJet, the work process was comprehensively optimized. Today, a total of 80 machines are placed in the small and large packaging departments. In the small packaging
department, the PaperJet produces cushions in a dispenser at the packing table, while in the large packaging department, the employees remove the cushion directly from the machine. The central preproduction of foil cushions and subsequent distribution to the packing stations has thus been replaced.
“Packing is now much more versatile than before,” says Scholz. The freely selectable cushion lengths allow for precise void fill. “The short set-up time is a crucial point which makes the PaperJet so attractive. We currently change the material pallet per workstation about every 3 to 4 weeks. This means a considerable timesaving compared to the previous 1 to 2 roll changes of foil material per day,” says Karg. This is achieved thanks to the ComPackt endless pallet in space-saving fanfold format, which offers 7,600 meters of recycled paper in a small footprint. “For an ergonomic workplace, our in-house perforated plate was integrated into the container solutions on request, so that all necessary materials are placed directly and ergonomically within reach at the packing station,” adds Karg.
The Hoffmann Group does not only pursue the goal of sustainability in the selection of the cushioning material. “Every year, we generate 600 tons of paper waste, the majority of which comes from incoming goods,” explains Karg. Previously, the waste was collected in several presses, which were then picked up separately for disposal. Now the waste paper is pressed in the company’s own bailing compactor.
These bales can be used by Papier Sprick to produce more paper for the PaperJets used in the LogisticCity. This is done at the Papier Sprick paper mill in Diemelstadt and provided through the
regular material deliveries. The result of the cooperation between the Hoffmann Group and Papier Sprick is thus not only a modern, efficient packaging solution, but also a sustainable recycling
management.