AutoLoadBaler is a R(e)volution
31st October 2022
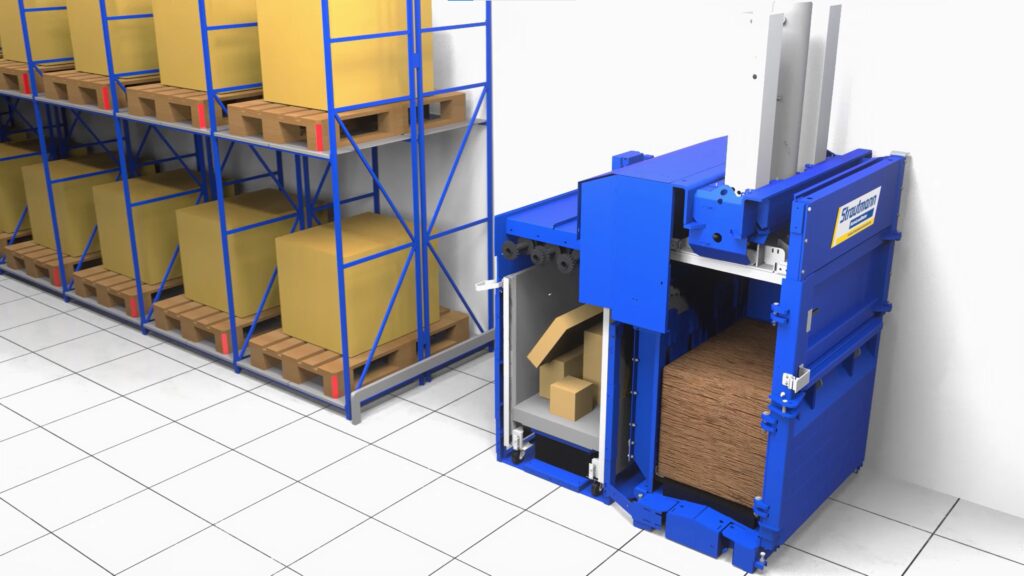
What to do with all the cardboard that accumulates in a supermarket every day? That’s an important question in the world of food retail. There are hundreds of cardboards of various sizes that arrive every day and must be disposed of. The immense amount of required work for this has been transformed into a simple process with the AutoLoadBaler, a r(e)volution of a baler from Strautmann Umwelttechnik.
The employees throw the cardboard into the collection cart. When it’s full, the collection cart is simply pushed into the press. The AutoLoadBaler empties the collection cart, and the baling chamber is filled automatically. After that the material is compressed with a pressing force of around 53 tonnes into a bale that can be sold directly.
After two to three days at the Rewe Wutke store, a bale weighing 400kg accrues. The bale is tied off with four wires. Even inexperienced people can strap the bale without any effort using the equipment supplied. Thanks to the convenient and safe bale ejection, the tied bale can simply be placed on a pallet for transport and transported away with a lift truck.
What sounds easy in theory also passes the practical test. At least that’s what Alexander Wutke, owner of the Rewe market Wutke in Bad Heilbrunn in Upper Bavaria, confirms: “The press is so important for us, and it makes work a lot easier.”
There are 22 employees in his store who ensure that the customer feels comfortable in the store and that they receive expert support if they have any questions or requests. They can now devote more time to this – their actual – task, since filling of the baler and time-consuming shredding and stacking of cardboard is no longer necessary. The cardboard no longer has to be re-sorted in the head office but can be handed over directly for recycling and thus fed back into the material cycle.
“We used to have to tear the boxes apart by hand, load them onto the roll containers and then throw everything into the press ourselves,” recalls store manager Michaela Markreiter. That took a lot of time and was quite exhausting. It was not uncommon for hands to be cut by razor-sharp edges.
In order to keep small cardboard boxes from falling out when they were collected, the ‘trolleys’ were wrapped in film. Often the collected cardboard also caused space problems, and everyone in food retail knows how valuable warehouse space is.
In the Bad Heilbrunn Rewe store, these efforts have been important; that’s why Wutke wanted to use the AutoLoadBaler right from the start: “I knew it would change our whole situation,” he recalls. The 36-year-old completed his training and various departments at Rewe and has found that conventional baler always requires a lot of extra work, which takes time and, of course, causes costs.
“We could hardly cope with the number of boxes that accumulate with the fruit and vegetable deliveries in the morning alone,” says Wutke. “With the AutoLoadBaler, we do not only increase the profitability of the operation, but also the satisfaction for our employees because a lot of stress is eliminated. Even a loss of staff can now be better dealt with, since some time-consuming work steps are no longer necessary.
“The AutoLoadBaler’s collection cart are easy-to-move – much better than the collection trolleys. While one collection cart is being emptied in the baler, two more are in use in the store, so there is no waiting.”
“The faster work is also reflected in the shop and that ultimately benefits the customer,” says Markreiter. All in all, she and her boss think things just look tidier in their 970 sq m supermarket and in the warehouse. A further smart detail is that the side walls of the collection cart can be used as advertising space, either for the market itself or for local companies.
The press itself is 3.05m high and requires only 4.5 sq m of floor space. Pushing the filled collection cart into the side of the baler is uncomplicated and effortless. The closed system ensures a high level of operator safety. There is a detailed briefing for the employees and once a year a service employee comes for maintenance.
“Up until now, everything has always been flawless,” says Wutke. He’s a fan of the AutoLoadBaler, his ‘baby’, as he says jokingly. “This baler is the best thing Rewe could have done for me. I can only recommend it.”
The AutoLoadBaler revolutionises the cardboard disposal process in all retail, logistics and manufacturing applications. Time-consuming filling work that previously had to be done manually is now done automatically. It is no longer the operator but the intelligent system that monitors and controls both the filling of the baler and the compaction.
Practical experience and studies show a saving in working time of up to three hours and 43.5 minutes per bale – this corresponds to an increase in productivity of over 800%. The automation results in even, stackable bales weighing more than 400kg, which can be marketed directly to the paper mills.