What can the Logistics Sector Learn in 2021?
25th January 2021
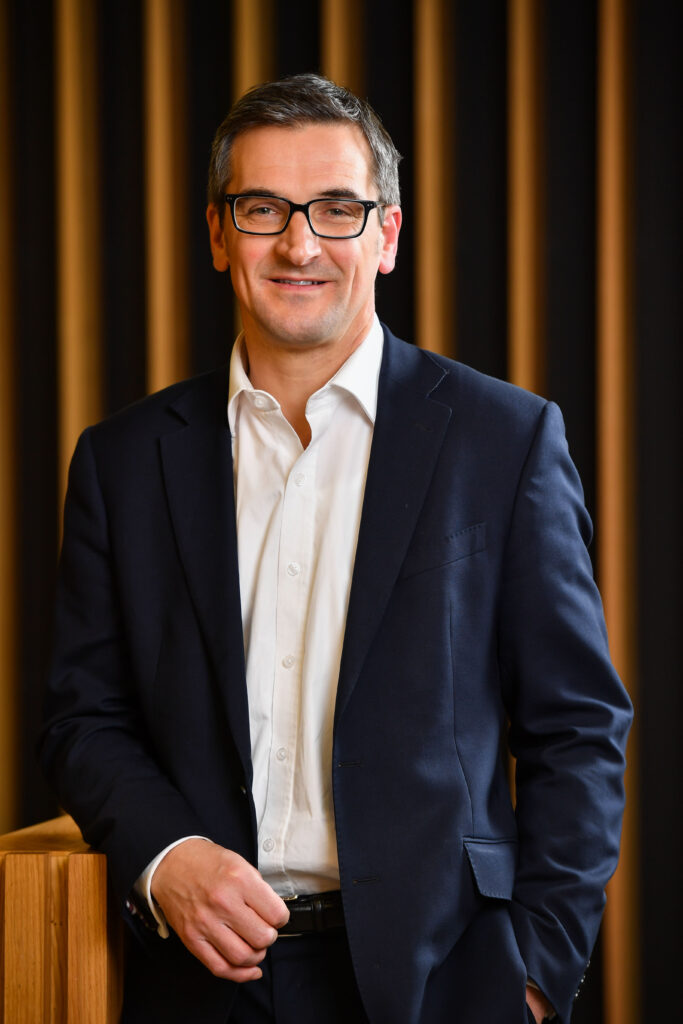
2020 was a year of extremes – particularly for logistics businesses, where a global pandemic polarised the sector, creating both winners and losers depending on how end-user markets were impacted. Some were forced to reposition themselves in the wake of COVID-19, while others had to positively adjust to manage a sharp increase in volume.
Against the unexpected backdrop of coronavirus, the long and drawn-out saga of Brexit has sat heavily on the sector’s shoulders – two uncertainties that combined have piled considerable pressure on the industry.
So, as the page is turned on 2020, what are the key takeaways from last year and what can we expect from the next 12 months, writes Jason Whitworth, M&A Partner, BDO
2020 – a year like no other
COVID-19, economic disruption, uncertainty surrounding our future trading relationship with the EU, and underlying issues around driver shortages and skills, have created significant upheaval in the UK logistics market. Battling on all fronts, it’s hardly surprising that the sector remains pessimistic about the state of the market, with our recent Barclays-BDO Confidence Index falling from 49.7 in 2019 to 47.1 in 2020 – its lowest level since the survey began in 2012.
Given the unprecedented impact of COVID-19, perhaps the only surprise is that last year’s fall in confidence was not more pronounced. This is particularly so when you consider that more than two-thirds of logistics companies (67.1%) said trading was tougher in 2020 and almost a quarter (24.2%) said market conditions are much more difficult than in 2019 – the highest proportion since the second half of 2012.
As with so many other industries, COVID-19 has shaken up the logistics sector by rapidly accelerating a number of existing trends. This includes the move to e-commerce and manufacturers increasingly going direct to end consumers – not to mention the disruptive effects (both positive and negative) on demand, as well as on supply chains. This was clearly visible amongst those focused on e-commerce, last-mile deliveries, pharmaceuticals and healthcare, which fared relatively well; others operating in manufacturing sectors, such as automotive, saw unprecedented levels of disruption. 2020 really was a year like no other.
Industry reset
Amongst all the upheaval, the industry has been forced to reset and, from that, we have seen a number of positives. This includes an unwavering commitment to the green agenda, with companies continuing to focus on environmental investment, despite the pandemic. The top ‘green’ areas include optimising fuel used by existing fleets; recycling initiatives; warehouse-related improvements, such as installing LED lighting; and introducing and expanding alternative energy vehicle fleets. This is in response to increasing numbers of city clean air zones, which impose a charge on non-compliant vehicles.
What was particularly evident in 2020 was the acceleration of new technology adoption – whether that was replacing and upgrading current systems, such as those used for transport management (TMS), warehouse management (WMS) and Enterprise Resource Planning (ERP), or investing in new applications and technology, with particular focus on automating warehouses to tackle ongoing skills and labour shortages, while simultaneously increasing efficiency.
Coupled with that, there was a strong focus on staff management and wellness during the pandemic. In fact, nearly two-thirds of respondents (63.3%) in the Barclays-BDO Confidence Index Report said they now run wellness programmes for staff and, encouragingly, these appear to be playing some part in addressing the skills and talent shortage.
Of those who offer wellness programmes 79.3% said they have experienced reduced staff absenteeism, 56.9% reported higher productivity and performance from employees, and well over half (55.2%) said it has led to people staying in their jobs for longer.
Challenges ahead in 2021
While a focus on staff management and wellness has clearly had a positive impact on retention, the perennial issue of skills and talent will continue to pose a significant challenge for the logistics sector in 2021. Once again, up there at the top is the enduring lack of skilled drivers which has plagued the industry for many years. The knock-on effect of the pandemic and Brexit combined has led to a reduction in the number of EU nationals in driver roles, which had helped to mitigate the issue in previous years. Government support with measures, such as funding for training and improved national facilities for drivers, is being sought to encourage UK workers to fill these vacancies. However, it is a concern over the number of warehouse staff that is the biggest shift in talent-related issues and one that has only been exacerbated by COVID-19 and Brexit. To alleviate these talent shortages, operators are working hard to attract more young people into the industry, improving pay and conditions and strengthening training.
As we continue to unpick the detail and understand the true meaning that the end of the Brexit transition period has brought, the way in which the industry responds and reacts over the next few months will prove vital. The deal announcement will have undoubtedly been met with some relief. However, what is very clear is that the post-Brexit world that we now find ourselves in will undoubtedly create greater inefficiencies through layers upon layers of additional bureaucracy. The Free Trade Agreement has established zero tariffs on goods but, with it, it has put up new barriers to the flow of goods, including fresh paperwork, customs checks, and health/standards checks for food and agricultural products and, consequently, added new costs to the expense of cross-border trading.
The key is preparedness, although this may depend on the resources of the business – with larger companies able to implement systems in advance more easily, and smaller distributors missing that support. The Road Haulage Association (RHA) estimates that 50% or more of small-to-medium-sized companies might not be ready for the border checks, and warns that much of the ensuing chaos will be invisible, with freight instead held up at distribution centres round the country.
At the end of 2020, we witnessed the immediate impact that a new variant of COVID-19 can have on export, import and international travel; that, combined with the ramifications of Brexit, will continue to pile significant pressure on international freight. Thankfully, at the time of writing this, there have been only a few instances of drivers not having the right paperwork. However, we are currently in the holiday season, the quietest time for trading in the year, and many anticipate delays as volumes increase later this month, with new post-Brexit customs systems largely untested. Reports that businesses have been stockpiling in anticipation of supply difficulties may mean less disruption in the short-term, with a longer curve before trading resumes at normal levels.
As such, queues, blockages and delays, may unfortunately become a familiar sight in the early parts of 2020 as we adjust to a new way of working. Richard Burnett, the chief executive of the RHA, has been very clear and outspoken about the challenges facing the industry, highlighting the need for 50,000 more customs intermediaries to handle the mountain of new paperwork after transition, with Government support to recruit and train those extra people ‘woefully inadequate’. He recently said: “We know that traders and haulage operators will face new customs controls and processes and we know that if they haven’t completed the right paperwork their goods will be stopped when entering the EU.”
There will also be other important wrinkles to iron out as the detail of the agreement is absorbed. Not least with the reduction in cabotage, with large trucks restricted in the Free Trade Agreement to three movements within the EU before returning to the UK. This will restrict the ability to tramp across the EU, impacting specific markets such as live events. With 85% of European concert logistics businesses currently based in the UK, without an exemption this may present barriers in European touring – a sector already struggling following the pandemic.
What is interesting to see is the tendency of Brexit to polarise views: ranging from predictions of chaos, excessive paperwork and higher prices for vehicles and parts, to potential new opportunities as UK businesses adjust their supply chains and inventory levels and require new logistics operations to serve their customers.
With change comes opportunity
So, as we embark on a new year, the focus has shifted once again to adapting to the new constraints and market conditions, and recognising the opportunities that are emerging.
COVID-19 and Brexit aside, fulfilment e-commerce is clearly here to stay, and it presents existing and new players with a perfect platform on which to build upon the success that has spawned from 2020.
For more insight into the logistics sector, you can sign up to our newsletters here.