IFOY FINALIST FOCUS: Extension of Hase Safety Gloves’ automated warehouse by STILL
31st May 2022
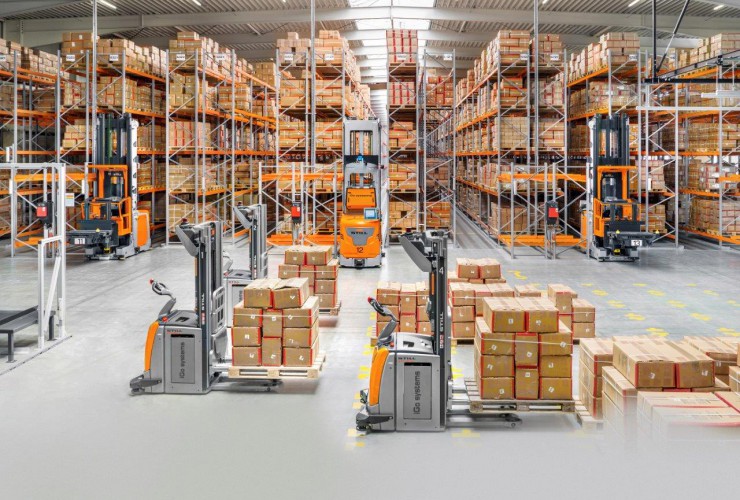
Our second finalist in the Integrated Warehouse Solution category of the IFOY Award – which we are showcasing ahead of the winners announcement on 30th June at BMW World – is the extension of the automated warehouse of Hase Safety Gloves GmbH by intralogistics expert STILL.
IFOY category: Integrated Warehouse Solution
Hase Safety Group sets course for growth: Automated industrial trucks are also very flexible in combination with variable goods transfer. One example is the expansion of the automated warehouse at Hase Safety Gloves GmbH. There, the STILL industrial trucks were replaced by new automated, more powerful vehicles with telescopic forks. Newly programmed route optimisations also contribute to the increase in performance. STILL expanded the racking system to a total of 10,000 pallet spaces.
Customer: Hase Safety Gloves GmbH
Realisation Phase:
From: 2021-05-31
To: 2021-10-30
Description
For more than 70 years, the production of work gloves has been the core business of Hase Safety Group AG in the Frisian town of Jever. In 2013, the German company celebrated 75 years of company history. Due to the growth of the Hase Safety Group, the existing space and handling capacities were no longer sufficient. The task was therefore to achieve greater storage and transport efficiency. One particular challenge was the conversion during ongoing operations. Until today, the course is clearly set on growth. That is why an extension was recently built. It houses new logistics areas, an innovation centre for customer training, product development and product presentation.
Theodor Wagner, CEO of Hase Safety Group AG, emphasises: “This is the only way we can meet the growing demand for new products. More turnover of goods for our Europe-wide customer business also requires more storage capacity as well as efficient and economical warehousing.”
More productivity through more automation
To keep distances short, the various glove articles are packed in cartons and stored neatly by type on pallets in the narrow-aisle warehouse according to the ABC analysis. For safe and independent movement of the vehicles, all AGVs (Automated Guided Vehicles) navigate with rotating laser scanners that constantly measure the distances to the installed reflectors. Three MX-X very narrow aisle trucks and six EXV-SF high lift stackers of the latest generation were each equipped with STILL’s iGo Systems automation kit.
At the goods receipt of an overseas container, the cartons with new goods are palletised by Hase employees using a telescopic conveyor belt and a vacuum lifting aid and distributed to the goods receipt locations according to type. Maximilian Engels, project manager and IT administrator at Hase Safety, explains: “We largely automated the processes in the goods receiving area. By manually scanning the storage locations as well as the articles, the automated storage processes are now triggered in our IT system.”
EXV high lift stackers pick up the finished pallets and drive them through the contour check. There, the pallet is measured to see if it is too long, too wide or too high. If successful, an EXV moves the pallet to the transfer rack in the narrow-aisle warehouse. There it is picked up by one of the automated MX-X high-bay stackers and stored in the assigned storage location.
In the case of a retrieval, an MX-X transports the respective pallet to the transfer station. The pallet is then picked up by the EXV and transported either to the transfer rack of the manual picking warehouse or directly to the shipping lanes of the trucks. Once the storage and retrieval operations have been completed, the AGVs automatically move to their waiting positions. All MX-X are equipped with telescopic forks, as the aisles at Hase are significantly narrower and thus not suitable for high bay stackers with swivel traverse forks. By using telescopic forks, both the storage density and the storage capacity are higher.
Identical components, controls and interfaces turn the trucks into high-performance AGVs. “One effect of the route optimisations is a lower number of transport orders and, as a result, less movement of the AGVs. This has also significantly improved safety in the warehouse. Thanks to the close cooperation between our team and the STILL project managers, we were able to successfully reorganise both the software and the hardware of our automated warehouse despite the Corona pandemic. Now we are well prepared for the challenges that lie ahead in the near future,” emphasises Maximilian Engels.
Autonomous charging of the vehicle batteries
The state-of-the-art photovoltaic system on the more than 10,000 quare metre-sized roof supplies green electricity to charge the forklift batteries. Lars Lemke, project manager from STILL’s Bremen branch points out: “To charge the batteries, the AGVs move to their charging stations independently. Without having to connect a cable, the battery is charged simply by contact with the ground. This is another highlight: because now the AGVs can charge their batteries autonomously at night and without additional personnel.”
One-shift operation still possible
The overseas containers from Bremerhaven are not only delivered during the day, but also in the evening. The experienced entrepreneur Theodor Wagner clarifies: “With the reorganisation of our automated warehouse, we can now also carry out automated storage in the evenings or overnight without the need for staff. This is an important requirement for the new processes. Even with constantly increasing demands on the market, we can continue to maintain our one-shift operation with the new system.”
Maximum flexibility in the scalable automated warehouse
Due to the scalability of the automated warehouse, it is possible to react quickly and flexibly to larger capacity requirements with additional AGVs. For the demand in the near future, a total of 10,000 pallet storage locations are now available. The fact that the AGVs can also be operated manually for special storage processes underlines the flexibility of the automated warehouse.
Summary
With the iGo automated warehouse from STILL, the modern distribution centre is ideally equipped to meet the future requirements, including those of other medium-sized companies. Customer requests and the requirements of major customers are thus fulfilled and the products are delivered across Europe, promptly and in a timely manner. “The first wave of logistics automation started back in 2010, and in recent years we have steadily expanded our automated warehouse and brought it up to date with the latest project. For more than 30 years, we have had a reliable partner at our side in STILL, who very quickly turns our ideas into reality,” summarises Theodor Wagner. Once again it shows that automation is an issue for companies of all sizes and has now finally arrived in the SME sector too.
CLICK HERE to watch a video.
IFOY TEST REPORT
With the help of Still, Hase Safety Gloves has expanded the system of its automated warehouse and made the processes more efficient – during ongoing operations. Although four to five jobs were replaced by automating the system, 15 new jobs were created at the same time by expanding the warehouse by 200%.
80 employees, 70 of them at the headquarters in Jever, take care of incoming and outgoing work safety clothing at Hase Safety Gloves, which mainly arrives by container from the Far East. Of the 12,000 square metres of warehouse space at Hase, around 7,000 square metres alone are now automated, and of the total 13,000 storage spaces in the warehouse, just under 7,000 spaces can be attributed to automation. A 10,000 square metre photovoltaic system on the roof is also used to charge the forklifts used in the warehouse. Speaking of forklifts: Hase successfully operates according to the “mixed operations” principle: Forklifts and staff can meet each other, and the use of protective fences has been deliberately dispensed with.
When employees place a filled pallet on a place in the staging lane after goods receipt, this simultaneously means a transport order for a still unit – it goes off to the warehouse or cross-docking directly to goods issue. At Hase, there is automatic whole stock removal, but also manual order picking. Until this happens, the pallet first goes through a so-called contour check: a gate with a laser curtain that eliminates tolerances of the pallet so that the automatic warehouse does not store a “brake block” – otherwise the system stops. If an error is detected, the pallet is immediately forwarded to the “not right” location and the problem is eliminated. Hase uses three automated MX-X narrow-aisle stackers and six EXV-SF high-lift trucks of the latest generation, all of which are equipped with Still’s iGo Systems automation kit. The EXVs pick up the sorted palletised goods at the goods-in location and take them to the transfer rack in the narrow-aisle warehouse, where they are picked up by one of the automated MX-X units and stored in the assigned bin location. For retrieval, this process happens in reverse order. Once the AGVs have done their work, they automatically move to their waiting position.
A novelty for Hase: a changeover aisle in the middle of the system, which, together with a spray wall, replaces the otherwise necessary firewall, enables the forklifts to move simultaneously from one racking aisle to another without having to return to the beginning of the racking. In the manual area, the forklifts always run in single-shift operation. Overnight, they are then autonomously recharged according to the “opportunity charging” principle, using lead-acid batteries, which are more economical than lithium-ion batteries in this application. The racking aisles at Hase can be much narrower than is normally the case: compared to the use of high-rack forklifts with swivel reach forks, the MX-Xs equipped with telescopic forks require significantly less space, which has a beneficial effect on storage density and capacity.
Because the overseas containers from Bremerhaven are not only delivered during the day, but also in the evening, it is an advantage for Hase that with the reorganisation of the automatic warehouse, goods can now be stored automatically in the evening hours or at night without the need for personnel. This means that the existing single-shift operation can continue to be maintained.
IFOY Test Verdict
With its automation solution, Still has brought Hase up to the state of the art and made it fit for the future. With the iGo automated warehouse solution implemented at Hase, other medium-sized companies can also streamline their processes and bring them up to date. Automation, and this has been impressively demonstrated by Still, is a topic for (almost) any size of company.
IFOY INNOVATION CHECK
Market relevance: The expansion of existing warehouse locations is a frequent case in practice. Changes in the company’s own products or production processes, but perhaps even more so the changed behaviour of customers with a focus on product availability and short-term delivery, often make changes necessary. Both the structure and the processes can be affected by changes. The example at the Hase company shows a special case, as the possibilities for adjustments in the layout were very much limited by the available floor space for extensions. In addition, the owner put the unconditional will to automate first, whereas the economic efficiency of an application is the highest priority for most users. For the above reasons, the market relevance can therefore be rated as good, as the solution cannot be transferred to most extension cases without restrictions.
Customer benefit: Measured against its own objectives, the customer Hase has certainly achieved its goals to a high degree. With regard to the general case, however, a limitation to a good customer benefit results from the previously mentioned reasons.
Novelty: The specific expansion of the warehouse at Hase is well solved and the implementation with state-of-the-art vehicles is also at the current level of available technologies. The innovation results from the appropriate combination of the known well-functioning trades in a very limited environment. However, similar solutions could be achieved before with available equipment.
Functionality / type of implementation: The many limitations of the extension in the existing building were well taken into account in the realisation of the solution. The solution offers many functions for the operator and provides him with alternative uses of the vehicles as redundancy or to absorb power peaks.
Verdict: The expansion in the existing stock is impressive and the implementation with state-of-the-art vehicles is well solved. The innovation results from the good combination of the known well-functioning trades in a very limited environment.
market relevance +
customer benefit +
novelty Ø
functionality / type of implementation +
[++ very good / + good / Ø balanced / – less / – – not available]
For an overview of all the finalists, visit www.ifoy.org
CLICK HERE to find out more about STILL.