Shoe Sortation Solution
20th August 2019
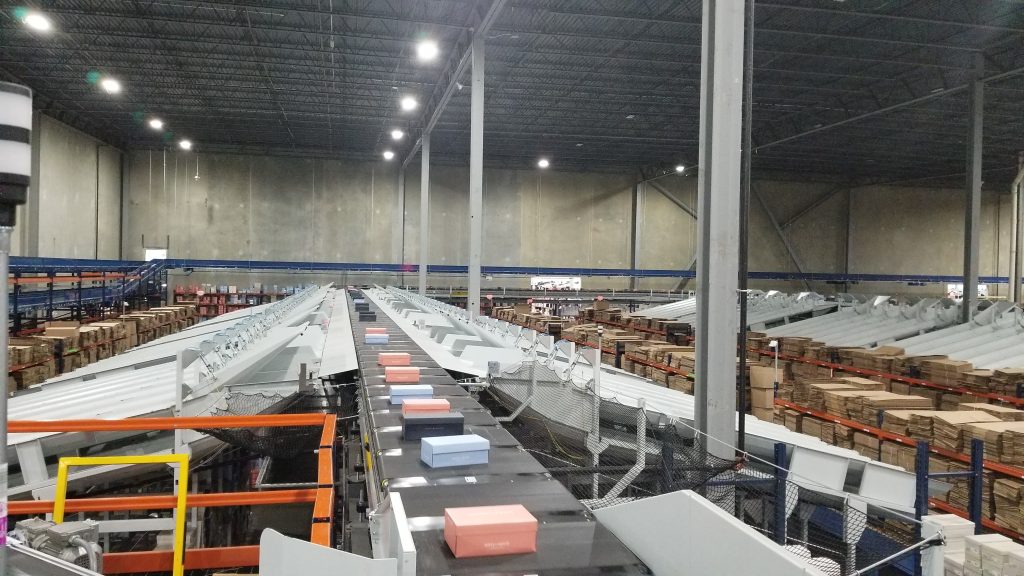
A modular material handling system for a new distribution facility in Cranberry, New Jersey for the end user Distribution Management Group Inc. (DMG) has been realized by Conveyor Handling Company (CHC). At the heart of this solution is the state-of-the-art crossbelt sorter technology from Interroll which reduces electricity costs, simplifies maintenance and makes product packing and distribution more efficient.
Since 1975, Baltimore, Maryland-based CHC has sold, serviced, and designed an impressive array of solutions for manufacturing companies, e-commerce and retail distributors, health care and clothing producers, and more. Past projects include crossbelt sortation systems, turnkey conveyor and racking installations, automated storage and retrieval systems, multi-tiered staging lanes, and even modular offices and mezzanines.
Despite this deep expertise, CHC recently faced an interesting challenge. One of its longtime customers, Distribution Management Group Inc. (DMG), was opening a new facility in Cranberry, New Jersey. The third-party logistics company (3PL) would be responsible for sorting, packing, and shipping products for its clients in the footwear industry and needed material handling equipment able to reliably process and ship 100 shoe boxes per minute.
“They originally wanted us to design a distribution center modeled after their existing facilities,” explains Rich Rittermann, Vice President of Operations at CHC. “In this instance, an employee would push a cart up and down each aisle, picking shoes as they went; when the cart was full, they’d move it to a central sorting area, where other workers would start pulling boxes off the different carts and packing them until each order was filled. There was nothing wrong with their process, except that I knew it would be too labor intensive and eventually become unmanageable at the volumes they were anticipating. They needed an automatic sortation system, and it was my job to convince them of that.”
Rittermann had previous experience with such systems, but the combination of high product volumes and the need to sort color, size, and style combinations by the hundreds led him to consult with the Interroll team, who told Rittermann that they were working on a shoe distribution center in Mexico, and agreed that Interroll’s horizontal crossbelt sorter would be an ideal solution.
Unlike traditional crossbelt sorters, Interroll’s solution uses a pneumatically actuated plate and drive wheel mechanism rather than a motor on each carrier to transfer goods to the appropriate chute. This reduces electricity costs and simplifies maintenance to increase reliability and the gentle motion means the sorter can be used with delicate products like eggs and yogurt and it still being powerful enough to move heavy sacks of grain or animal feed.
The system is both smart and accurate, with automatic recirculation of “no-reads” and overflow products. This is especially important in e-tail, where system demands are unpredictable, and customer return rates are much higher. The horizontal crossbelt sorter is also smart about floor space. Its modular design is compact yet easy to reconfigure based on changing needs. In this particular application, CHC “double-stacked” the conveyor, maximizing the system’s throughput without increasing its footprint.