New Vertical Buffer Module Speeds Up Small Parts Picking
10th November 2016
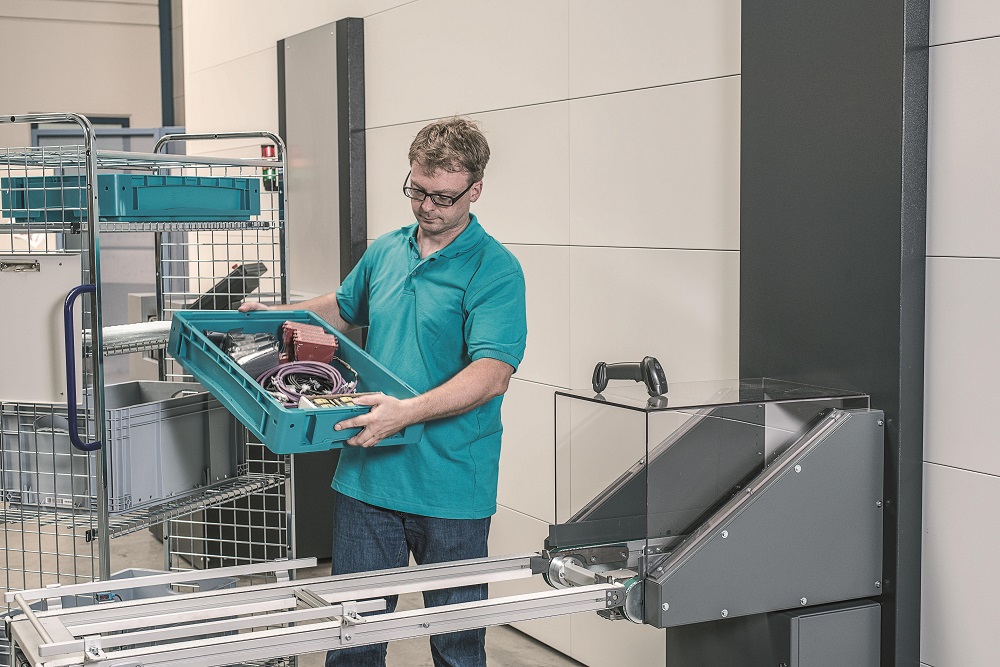
Intralogistics specialist Kardex Remstar UK has launched its LR 35 Vertical Buffer Module onto the market as part of what it calls the new generation of its highly efficient storage and picking systems.
The Kardex Remstar LR 35 is the perfect solution for any company involved in handling single-part or small-volume orders – providing fast and accurate access together with secure storage. The LR 35 can speed up performance, enabling up to 500 order lines per picking station an hour, and is ideal for picking small parts from bins, cardboard boxes, and trays in small and medium-sized warehouses. The unit design consists of a shelf system with automatic bin handling, picking stations, and its own logistics software.
We are extremely proud of the new LR 35. It has been designed to deliver high performance when selecting parts and offers our most advanced picking solution to date, said Tom Findlay, Sales Director for Kardex UK and Ireland. We are seeing developments in our industry particularly with the growth of online distribution and a need for solutions that provide greater efficiencies and accuracy in both B2B and B2C. I believe the demand for greater dynamism, ergonomics, and energy efficiency in intralogistics will only grow further and here at Kardex we continue to develop solutions that will meet the changing needs of our customers.
Better performance thanks to the Kardex innovative replenishment design – The LR 35 uses its own state of the art replenishing solution and each station can be fitted with several access openings in different designs. At the heart of each station is the turntable. Tilted at an angle of 20 degrees, it has been ergonomically designed to guarantee stress-free working. While the operator picks one order, the LR 35 prepares the next bin and places it on the rear shelf of the turntable. As soon as the picking process is complete the turntable turns through 180 degrees and the next bin is ready for picking. This permanent access to goods keeps waiting times to a minimum and goods can be stored in standard mini-load systems compatible bins. Each load carrier can hold up to 35 kg.
Energy-efficient by design – The LR 35 features lightweight design throughout. The unit consists of a shelf system with an aisle. Within the aisle, a movable mast with a rotating gripper loads the picking stations. Reducing the number of components and using state-of-the-art technology not only guarantees the scalability of the unit, but also saves a significant amount of energy. The LR 35 only consumes a third of the energy of a mini-load system, and thus dispenses with the need for recovery energy systems. Modern drive technology, highly efficient motors, and optimally configured frequency converters also contribute to the energy-saving concept. In addition to the environmental benefits, the LR 35 slots seamlessly into existing processes and can be adapted to fit individual buildings, linking to existing conveyor technology with no extra effort. The conveyor connection can be fitted on the front, rear, or end face of the unit. The LR 35 comes in a variety of versions, designed to meet the evolving needs of companies. All versions of the LR 35 are based on the same components and technology.
The architecture of the unit software has also been updated in line with the latest technology.