Shuttle racking system for pallets : Space-saving storage for large quantities of goods
3rd June 2015
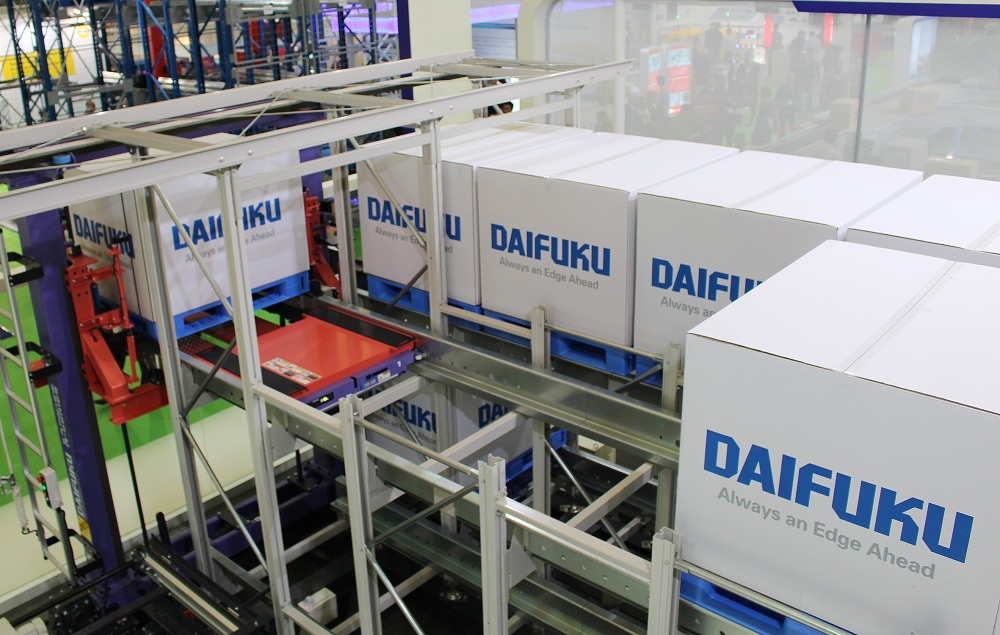
The demands on a warehouse are clearly defined: it shall be compact, shall enable efficient processes and must have a high cost/benefit ratio. With this in mind, the shuttle racking system is an efficient method of storing pallets, saving both space and resources. This applies in particular to industries in which large quantities of goods are stored. During an interview, Werner Gubesch, Manager responsible for Engineering in Europe at DAIFUKU CO., LDT., explained what in detail are the benefits of shuttle racking systems and what will be the direction of future developments.
Reporter: Mr. Gubesch, the shuttle racking system is becoming more and more popular. What are the main reasons for this development?
Werner Gubesch: Fundamental requirements to intralogistic systems from the early beginnings are optimization of space requirements and reducing costs. Especially in industries with continuous growth, such as the food industry, the need for efficient solutions has steadily increased in recent years. Companies are facing consistently increasing handling rates, meanwhile the delivery times are becoming shorter and shorter. Such requirements define the demands on future storage systems. Everything has to become more compact, faster and more efficient. Shuttle racking systems are extremely efficient in terms of volume utilization. Whereas in conventional high-bay warehouses only single or double-depth storage is possible, in a shuttle racking system pallets can be stored multiple deep, one behind the other. This increases the storage density and reduces the cost per pallet location. At the same time the wide variety of shuttle-based concepts can lead to an optimized usage of storage equipment in order to guarantee a significant faster access to the goods than it was previously possible with conventional shuttle racking systems. As a consequence handling rates within the warehouse can be increased to match current and future market requirements. Another important aspect is the high ROI factor. In addition to relative low investment costs for installation, the running costs of such a warehouse during the operational phase represent a very economic solution. Finally the system pays for itself after just a few years.
Reporter: What are the main benefits of such storage systems in practice?
Werner Gubesch: The operational processes in a shuttle racking system are as simple as they are efficient. Because the pallets can be stored multiple deep in the channels, the number of aisles can be reduced correspondingly and as a consequence fewer storage and retrieval machines are needed. Companies thus benefit from cost savings. Most of the work is carried out by shuttle vehicles. They travel straight into the channels, pick up the pallets and transport them to the storage and retrieval machines. These then carry the goods to the pre-storage area. By separating the shuttle movements from the storage and retrieval system, more orders can be processed simultaneously in the same amount of time. This increases the throughput significantly. A wide range of possible combinations between shuttles and storage & retrieval machines can be utilized in order to meet customer requirements in the most adequate and efficient manner. The availability of the system and the throughput rate can be flexibly controlled. The scalability of the systems also enables users to adapt their warehouse to suit changing requirements at a later time for example by adding or removing individual vehicles.
Reporter: How do you think the market will develop in this area and what trends do you expect to see?
Werner Gubesch: The benefits of the shuttle racking system speak for themselves. Due to this we anticipate a number of interesting projects in future, for example in the food industry. After all, this is a highly competitive sector. As a consequence the intralogistic concepts and corresponding equipment has to be adapted continuously in order to meet more stringent requirements in the long term. When considering the current trends, there is no alternative to the usage of flexible shuttle systems operating independently from carrier vehicles. In practice this means several shuttles working in parallel to serve a single storage and retrieval machine. The advantage of such a concept is that the time consuming storage movements within the channels are fully autonomous. The storage and retrieval machine only needs to pick up the pallets one at a time. This reduces or even eliminates the waiting times during which the storage and retrieval system is positioned in front of the channel, since the shuttles operate at a much greater frequency. At the same time, the warehouse becomes more efficient.
Reporter: Mr. Gubesch, thank you for this interesting interview.