Motion: the next dimension of hand-eye applications
7th September 2021
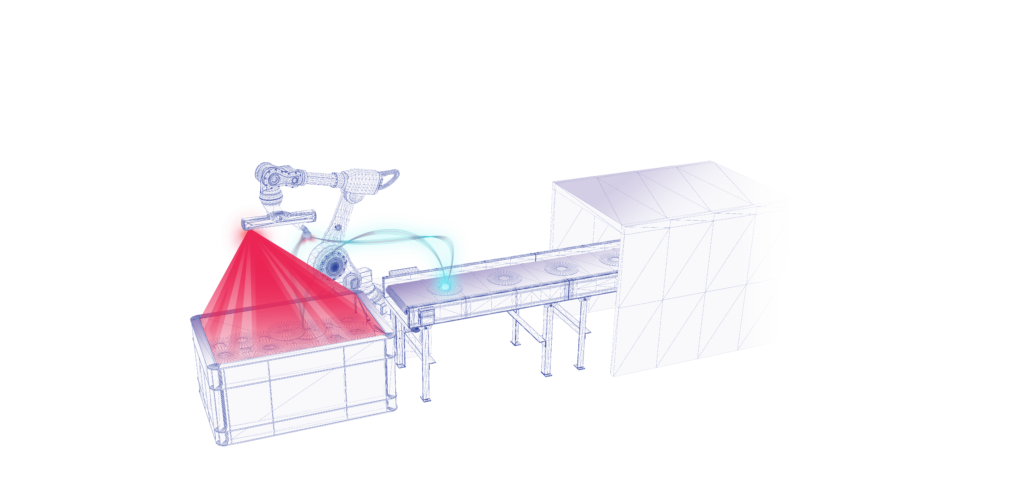
In robotics, a hand-eye system denotes a setup where a vision system is directly attached to the robotic arm, generally behind the very last joint. This approach offers an alternative to the more traditional fixed mounting of the vision system, usually above the working volume of the robot.
Though the hand-eye approach may benefit many applications, its potential has so far been largely limited by standard vision systems. Photoneo comes with an ultimate solution that finally puts an end to these vision-based limitations.
Advantages
The hand-eye approach is very useful in specific applications as it offers a number of advantages over the fixed-vision-system method. First of all, it can cover a much bigger scanning volume as it can be specifically directed to the area of interest, offering much more flexibility than the latter approach. The vision system is thus only limited by the reach of the robot rather than by its own scanning volume.
Scanning distance is one of the main parameters that determine scanning accuracy – a hand-eye vision system with a shorter scanning range can provide a much higher level of detail than a fixed vision system with a large scanning distance. If a customer has a large bin filled with small parts, the highest level of detail will be achieved by using a small scanner with a short scanning range mounted to the robotic arm.
A hand-eye system is also an advantageous option in case an application comprises two or more containers. A standard setup with a fixed vision system would either require a linear axis above the bins or multiple vision systems. A hand-eye system will do with one scanner moving with the robotic arm from one container to another.
Furthermore, bin walls or a vision system mounted above the container in a fixed manner may cast shadows on certain sections of the container, inhibiting proper scan acquisition of some parts. In such cases, a compromise needs to be made for finding an optimal position for the scanner in relation to the bin and sometimes the parts need to be manually rearranged. The hand-eye approach can easily overcome this challenge.
Hand-eye systems present a modern approach with rising popularity, which gains a firm foothold in an increasing number of robotic applications. Its benefits become even more important with the rise of collaborative robotics. However, one should keep in mind that the deployment of the hand-eye approach makes real sense only in specific types of applications.
Important considerations
Though the hand-eye setup provides a number of advantages, there are certain factors that need to be considered before adopting the approach.
Hand-eye systems require a more difficult installation than setups with a fixed vision system. It is also more difficult to find an optimal way to handle the cables that power the deployed vision system.
In addition, because the scanner is attached to the robotic arm, it may restrict the robot’s movements. It is therefore advisable to use a smaller vision system.
Another drawback of hand-eye systems is a higher risk of colliding with the sensor and possible difficulties with finding the optimal position on the robotic arm for the vision system, especially if it is of a larger size.
Moreover, robot movements cause vibrations, which standard high-accuracy area-scan vision systems cannot handle. Because of this, the robotic arm needs to stay still during scan acquisition, which may prolong the cycle time. As a result, the hand-eye approach is not the right solution for time-critical applications.
Of course, there are applications where the hand-eye setup is the best option and that do greatly benefit from this approach. In those cases, the vision-based limitations can be overcome with Photoneo’s revolutionary ‘Parallel Structured Light’ technology.
Hand-eye coordination in motion
The ‘Parallel Structured Light’ technology, implemented in the Photoneo 3D camera MotionCam-3D, enables hand-eye coordination without trade-offs between quality and speed. MotionCam-3D is the only 3D vision system that provides high-quality scans even during the movement of the robotic arm. The camera is highly resistant to vibrations and does not require stopping the robot.
The technology enables the capture of objects moving up to 144kmh, providing a resolution of 0.9Mpx and an accuracy of 300–1250μm, and in the static mode a resolution of 2Mpx and an accuracy of 150–900μm. MotionCam-3D is available in five models – most suitable for hand-eye applications are models S, S+, and M.
The greatest benefit of the novel technology is that the robot does not need to stop to make a scan, which dramatically shortens the cycle time when compared to standard technologies. It thus opens the door to new applications such as instant tracking of the object position.
Collaborative robotics has also been limited by the drawbacks of standard methods. Collaborative robots are slower per se than industrial robots and when combined with the hand-eye approach, the cycle times are prolonged even more. MotionCam-3D overcomes this limitation and works perfectly also if attached to the arm of a collaborative robot.
Motioncam-3D comes as an ultimate solution for any kind of robotic tasks. Vision-system-based limitations of the hand-eye approach are now an issue of the past. The technology offers the best resolution and accuracy for scanning at fast speed, effective resistance to vibrations, and shorter cycle times than ever.