Egemin supplies automated warehouse system with AGVs to Kim’s Chocolates
9th January 2015
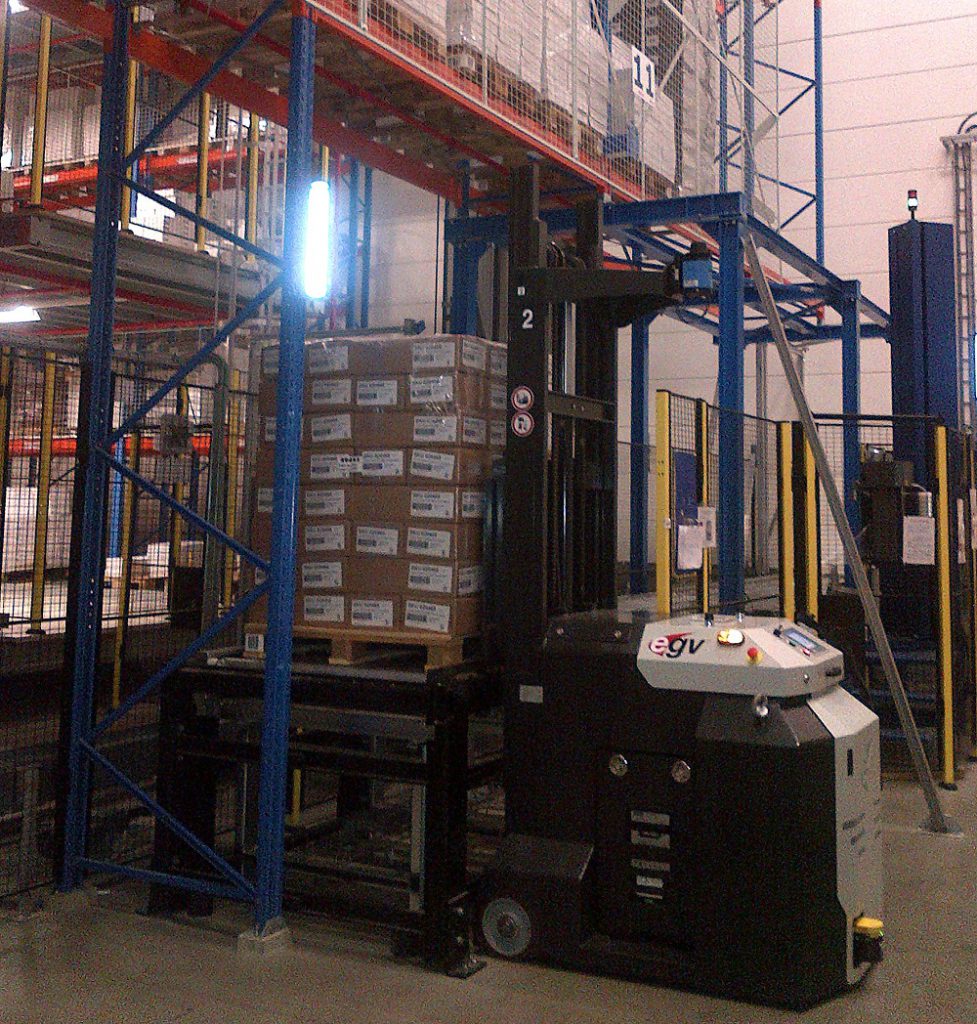
Egemin Automation has installed a fully automated warehouse system at Kim’s Chocolates for the internal transport, automated storage, and order picking of chocolate products. Egemin’s system includes three automated warehouses for the storage of semi-finished products, packaging materials and finished products. Three automated guided vehicles transport goods between warehouses and production.
Kim’s Chocolates, located in Tienen, Belgium, manufactures pralines, bars, and tablets, mainly for the export market. With this investment, the chocolate producer wants to increase its storage capacity, optimize its logistics flow, and support the expected growth.
AUTOMATED GOODS FLOW FROM A TO Z
- The warehouse system provides a turnkey solution for virtually the entire logistics flow at Kim’s Chocolates. It consists of the following components:
- Automated warehouse for storage of packaging materials with one curve-driving stacker crane
- Automated warehouse for storage of finished goods with one aisle-switching stacker crane
- AGV system with three counterbalance vehicles of type FLV3512/CL for goods transport between receiving, production, and warehousing and for intermediate warehouse storage for semi-finished products
- Voice picking system on three picking floors for the preparation of customer pallets with pralines
- Ewms® warehouse software for warehouse management and control of all internal transports
HANDLING OF PACKAGING MATERIALS
Incoming packaging materials such as wrappers, decorative boxes, and cardboard cartons are automatically transferred from the receiving zone to the packing warehouse by AGVs. The warehouse is equipped with a curve-driving pallet stacker crane that stores the supplied pallets in one of its two aisles. When packaging materials are needed in production, the E’wms® software gives a transport command to the crane to retrieve the required pallet from the warehouse and take it to the front zone. An AGV will then pick up the pallet from the front zone and bring it to the packaging line.
AGVS AS KEY TRANSPORT LINK
The three AGVs at Kim’s Chocolates play an important role in the logistics chain. In addition to the handling of packaging materials, they also take care of the transport of semi-finished pallets of pralines between production and the warehouse, where the AGVs temporarily store the pallets up to three levels high. The semi-finished pallets are stacked with boxes of one type of pralines. The AGVs then take the pallets to the sorting line where the pralines are sorted into assortment boxes. After sorting, the pallets of assortment boxes are transported to the finished products warehouse. Pallets with tablets and bars are directly transferred to the finished products warehouse.
QUALITY CONTROL AND PICKING
Product quality is a top priority for Kim’s Chocolates. To ensure product quality, the AGVs place pallets with finished products in a control rack in the finished products warehouse at regular intervals. After a positive quality check of the products, the AGV may take the pallet to the import conveyor of the warehouse. Here the pallet is wrapped and labelled and then automatically stored in one of the three aisles by the aisle-switching pallet crane. There are three picking floors in the distribution zone where operators put together pallets with tablets and bars using a voice controlled picking system that is controlled by the E’wms® software.