Automated vehicles to receive “trail maps” soon
29th April 2021
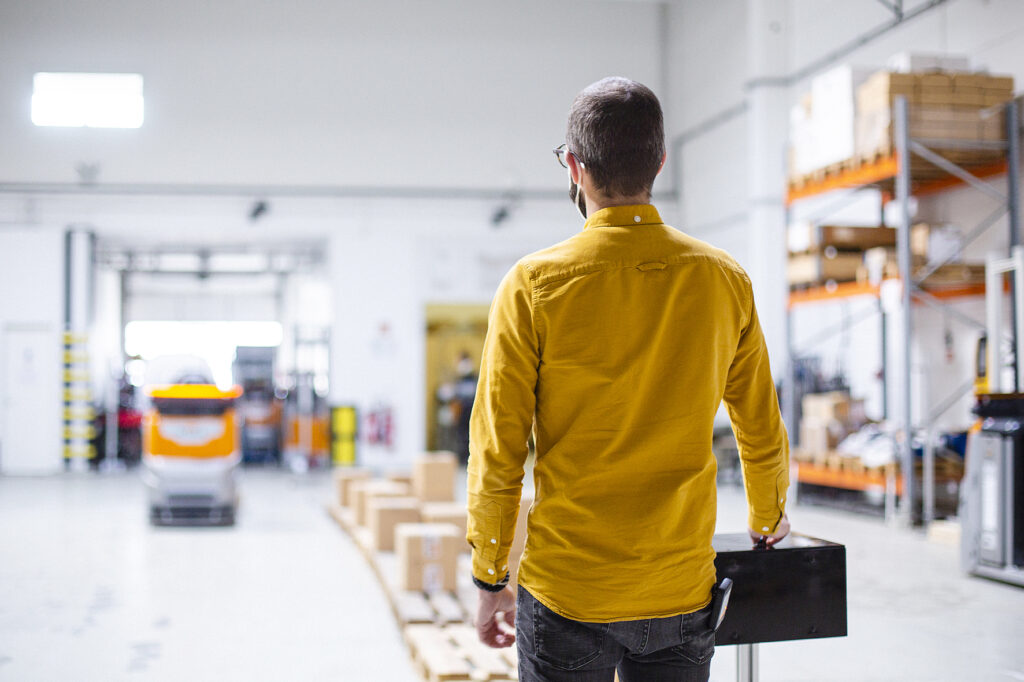
Hamburg-based intralogistics supplier STILL has taken part in a research project conducted recently to help map the future of automated vehicles.
In order to successfully automate warehouse processes, large amounts of data about the existing infrastructure are needed. How this information can be obtained more easily and possibly even standardised is one of the issues addressed by the “Industrial Indoor Localisation” (IIL) research project, which ended in February 2021.
The Hamburg-based intralogistics supplier STILL not only contributed their extensive expertise in the field of vehicle automation and robotics to this project, but with its autonomous horizontal order picker OPX iGo neo, they already have the ideal vehicle for efficient process automation, thus taking the next step towards greater autonomy and flexibility.
Indoor localisation offers intralogistics important tools for future-oriented automation solutions. However, only those who know exactly where a forklift truck, a robot or a pallet is at a certain point in time can exploit this potential.
“To determine this position, we need detailed maps that can be standardised as far as possible,” says Tino Krüger-Basjmeleh, robotics expert at STILL GmbH. This standardised reference framework was developed between 2018 and 2021 in the ‘Industrial Indoor Localisation’ research project funded by the European Regional Development Fund (ERDF) and the Free and Hanseatic City of Hamburg. The result is an open-source reference architecture for indoor localisation (RAIL) which facilitates the provision of location-based services. STILL was part of this collaboration between science (Hamburg University of Technology) and industry, as was the sensor manufacturer Pepperl+Fuchs.
Today, numerous automation projects are not realised only because their implementation always involves a significant initial outlay for map creation and vehicle commissioning,” says Krüger-Basjmeleh, describing the current situation and thus the background of the research project, adding: “At this point at the latest, there is a danger that customers will dismiss budding automation plans.”
In fact, great potential is being wasted in an important future market. To change this, maps are needed that enable man and machine to serve different needs and decouple complex developments. In addition, these maps should also be quickly and easily adaptable to the respective environment by non-technicians.
“If these prerequisites are met, intelligent localisation technologies will reduce costs, increase productivity and improve occupational safety in the near future. With the results of the IIL project that has now been completed, we have come a big step closer to achieving these goals,” asserts the robotics expert.
A key factor in the success of the IIL research project was the autonomous horizontal order picker OPX iGo neo contributed by STILL. “With the sensors already installed in the OPX iGo neo in series production, the integrated vehicle robotics system is already capable of answering all the questions that an automated vehicle has to answer,” describes Krüger-Basjmeleh.
It was these advantages that the vehicle brought to the research project. However, STILL and its customers can also derive important benefits from this circumstance. “In the course of the project, we developed many new capabilities for the OPX iGo neo and thus significantly increased its autonomy once again. This resulted in a new prototype of the vehicle, which we can use in future to demonstrate numerous automation approaches to our customers very clearly and without much effort,” says Krüger-Basjmeleh.
For instance, during the research project, the autonomous vehicle demonstrated for the first time that it can switch very smoothly and almost unnoticed by the operator between manual, fully automatic and autonomous assistance mode. In practice, these processes work like this: The vehicle reaches the picker in automatic mode with a previously picked up pallet and then switches to assistance mode. In this mode, it assists the operator in the picking process, so that the operator can individually assemble goods and the vehicle, as an “extended arm”, continuously follows the operator. At the end of the picking process, the vehicle automatically brings the order to the transfer point.
“This is indeed a novelty for the entire intralogistics industry. The fact that this process runs so smoothly is something we were able to demonstrate for the first time in the course of the research project. The operating personnel are optimally supported by this Cobot (collaborative robot) functionality,” says the robotics expert with satisfaction.
In summary, the IIL research project was a great success. For the further development of warehouse and production logistics – but also for STILL.
“At STILL, we have been working on automation for a very long time and can already offer our customers very efficient solutions. We would like to optimise these approaches further in the future,” says Krüger-Basjmeleh. However, it is always necessary to consider which products actually meet the customer’s needs and are ready for series production.
With the results of the IIL project, planning and commissioning processes can be simplified in the future, as the expert explains: “Thanks to the intelligent maps and the new vehicle capabilities, we will be able to install automated vehicles quickly and smoothly at the customer’s site in the future and discuss with them whether the proposed solution actually meets their needs. Thus, on the one hand, participation in such research projects helps us to increase customer benefits. On the other hand, it allows us to maintain our lead over our market competitors.”