IFOY Test Report: Youibot AT100
22nd June 2023
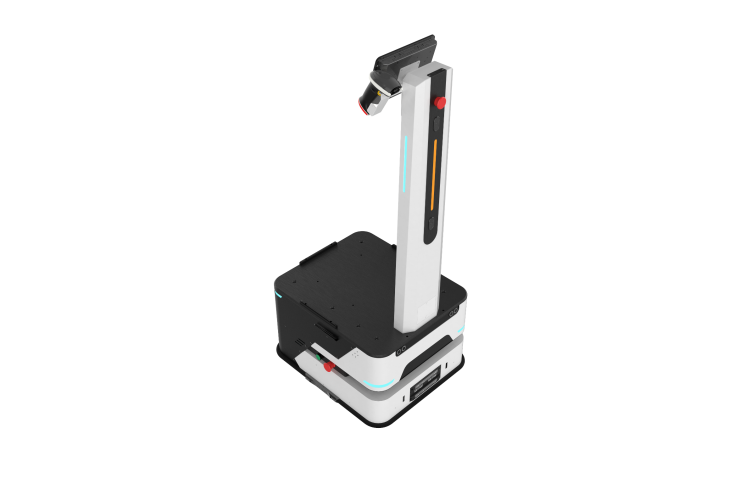
Tonight is the night when the winners of the 2023 IFOY Awards will be revealed at a ceremony in Dortmund. Alphabetically last, but certainly not least, we take an in-depth look at the AT100 warehouse fulfillment solution from Youibot Robotics.
Youibot’s Automatic Trolley warehouse fulfillment solution utilises its brand-new assistance picking robot AT100 AMR and its robot fleet management system YOUIFleet to integrate with retailers’ and 3PL’s existing infrastructures and workflow and help them meet their increasing fulfillment demand, while ensuring a low ROI.
IFOY category: Automated Guided Vehicle (AGV / AMR)
IFOY Test Report
Youibot’s Automatic Trolley (AT) solutions are an automated alternative to manual picking on trolleys. Depending on the use and height of the order totes, the number of platforms on the trolley can be adjusted. The AT100, nominated for the IFOY AWARD, has a load capacity of 100kg.
While manual picking involves pushing the heavy trolleys through the warehouse by hand which often results in lost time due to the partly long walking distances, the Youibot concept works on the principle of zone picking. Each picker has his own picking zone, which the automated trolley passes when one or more order lines for the respective orders on the trolley need to be picked in that zone.
The orders on the trolley are grouped by Youibot’s Robot Picking System (RPS), which is connected to the customer’s WMS. The RPS also controls the robots in a facility. By using a central fleet management system (YOUIFleet), the risk of congestion and waiting times is minimised. YOUIFleet supports a maximum fleet size of 150 robots at one location.
For safe navigation through the warehouse, the AT100 uses the latest SLAM laser navigation technology. Because the AT100 knows the warehouse better than any employee, the robot always chooses the most efficient route to the next picking zone. One employee looks at the touch display to see how many items are to be picked at which location, scans those items with the trolley-mounted scanner, and then the display shows which order bin the goods are destined for. Once all orders in a zone have been picked, the operator confirms this via the display and the robot continues on its way to the next picking zone.
If the multisensor system detects an obstacle or a person, the robot stops automatically and the green light (ready for operation) changes to yellow. The standard safety distance is 300mm, but if a higher travel speed is desired, this distance can be adjusted. The maximum travel speed of the AT100 is 1.5m/s.
The system is CE certified and also complies with the latest US standard (ANSI/RIA R1508). This makes it one of the safest systems in its class.
The AT100 is equipped with a Li-ion battery that ̶ when the robot is fully loaded ̶ is good for up to nine hours of use. Incidentally, the battery is fully recharged within one hour. This enables trouble-free 24/7 use.
In addition, the AT100 provides an efficient and error-free picking process. With the same number of pickers, up to three times as many orders can be picked. For the pickers, walking distances are significantly reduced. In addition, working with the robots is more pleasant and less tiring.
IFOY test verdict: With the AT100, Youibot offers a good example of how “You, I and a robot” can work together harmoniously and effectively. Its load capacity of 100kg is one of the highest on the market. The AT100 minimises walking distances and human errors. It offers higher efficiency and accuracy and guarantees a lower ROI.
IFOY Innovation Check
Market relevance: Picking support vehicles have a large market as they can be applied in many operations. Automated transport of the picked items for one or more orders on a vehicle frees the picker from the heavy-duty pushing of order collection totes. Instead, the pickers remain in defined zones of the picking warehouse, where they take over the item removals from the provided assortment as soon as a vehicle enters the zone with its assigned orders.
Customer benefit: The AT100 has large, individually adjustable shelves and a load capacity that makes it suitable for a wide variety of combinations of larger orders and item weights. All-important functional and safety elements are well integrated into the vehicle and arranged in an easily accessible manner. The vehicle is very robustly built for its task and enables a very high usability value for its users.
Novelty / Innovation: The structure and the compact design are not exceptionally new for a vehicle supporting order picking. However, the very good design with versatile adjustable shelves and the robust design, which seem appropriate for the application, make the unit stand out in this market segment. However, the software for controlling a fleet of AT100s is limited to routing the vehicles through predetermined zones and does not highlight the potential to guide vehicles and order pickers dynamically and thus order-dependently to each other in an order-picking warehouse.
Functionality / Type of implementation: The aforementioned features of the vehicle and fleet management offer good functions for increasing performance and ergonomics in order-picking warehouses. For the sometimes challenging operation in order-picking warehouses, the vehicle offers recognisable reserves in terms of stability and robustness.
Verdict: Picking support vehicles have a large market as they can be used in many businesses. The vehicle is robustly built for this task and promises very good benefits for users. The structure and compact design with adjustable shelves is not exceptionally new but offers good functions and features for the user.
Market relevance +
Customer benefit ++
Novelty / Innovation Ø
Functionality / Type of implementation +
[KEY: ++ very good / + good / Ø balanced / – less / — not available]