Warehouse Processes Optimised in the Cloud
16th March 2021
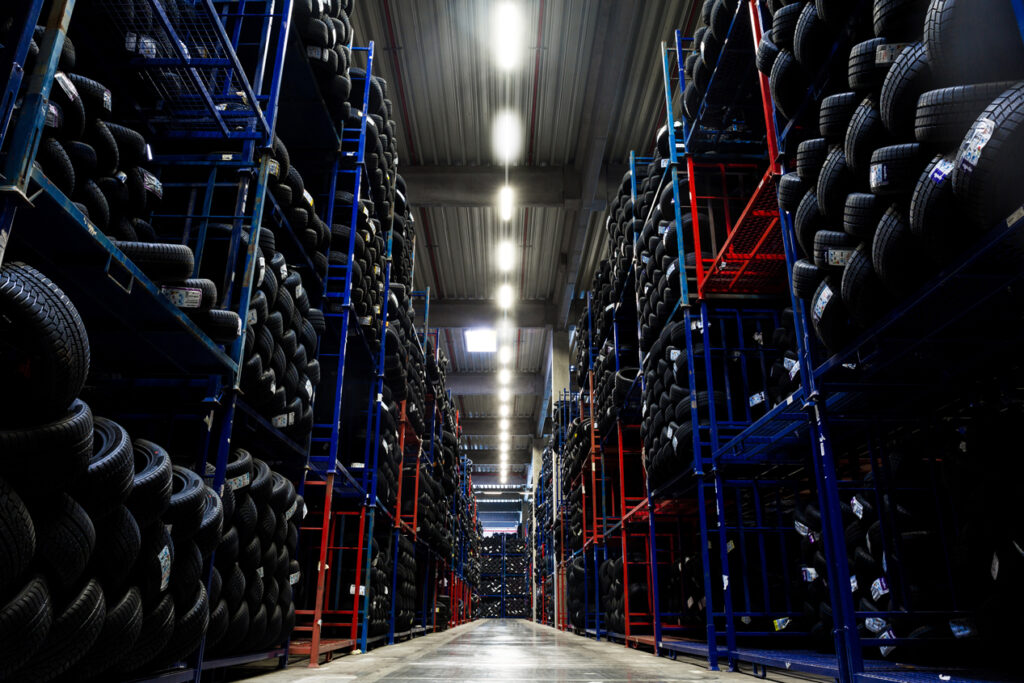
The reifen.com GmbH handles up to 60,000 tires and rims daily. With the EPG | LFS warehouse management system from EPG (Ehrhardt Partner Group), reifen.com has been optimizing its logistics processes in the warehouse for over seven years. After all, perfectly functioning logistics are a key prerequisite for the company’s success. Apart from the reifen.com online store, the multi-channel specialist has 37 stores in Germany and around 8,000 fitting partners internationally for additional services. reifen.com uses the EPG | LFS warehouse management system to automate processes, speed up shipping, minimize the number of returns and reduce costs. Currently, reifen.com has switched the hosting of its warehouse management system to EPG’s EPX cloud offering.
With order lists speed up shipping
reifen.com uses a dynamic batch formation function in EPG | LFS to bundle orders of the same type so that fast processing is possible. In this process, different customer orders are sorted according to a shipping type, for example, and combined into a picking tour in the outbound warehouse. This means that instead of labor-intensive piece picking, complete loading units can be removed and made available during packing, so that many different orders can then be processed quickly. The orders can then be processed without interruptions. The employees at reifen.com can define the batch lists very flexibly, e.g., according to shipping types, product groups or even destination countries. This significantly speeds up the shipping process.
Reduce costs for KEP service providers:By optimizing the shipping method for KEP service providers, reifen.com reduces shipping costs. Together with EPG, the existing shipping type determination was improved to automatically determine the most cost-effective KEP service provider in each case in the LFS.
Using simple controls to minimize the number of returns:
reifen.com uses a simple EAN check in the LFS for customer-specific quick packaging. Here, the employee in the shipping department additionally scans an EAN label, e.g. to check the correct goods or the correct quantity. This reduces sources of error and minimizes the number of returns.
For assembly stations, provide individual parts on time:
For delivery to end customers, individual parts such as tires, rims and valves must be picked and made available at assembly stations on schedule. EPG | LFS also ensures that employees are guided via walkways and that shipping is optimized. “With EPG, we have a very powerful software partner for managing our warehouse resources, picking and efficient shipping. The EPG helps us to further optimize processes and become even better for our customers,” says Jens Müller, Head of Logistics at reifen.com, summarizing the experience gained from seven years of cooperation with the EPG.
EPX-Cloud-Solution “Infrastructure as a Service”
reifen.com has switched the hosting of its warehouse management system to the EPX- cloud-solution “Infrastructure as a Service” offering. EPG takes over iSeries/AS-400 hosting and all IT services for EPG products as part of defined managed services. This includes operation, support and active monitoring of the systems, including data backup. The migration of the data to the EPX cloud was implemented over a weekend in less than 24 hours. “Thanks to the cloud solution, we can now flexibly scale the IT structures to ensure high performance and permanent availability,” says Hans Lechner, Head of IT, explaining the objective of the project.