Can WMS help Future Proof your Business?
21st August 2019
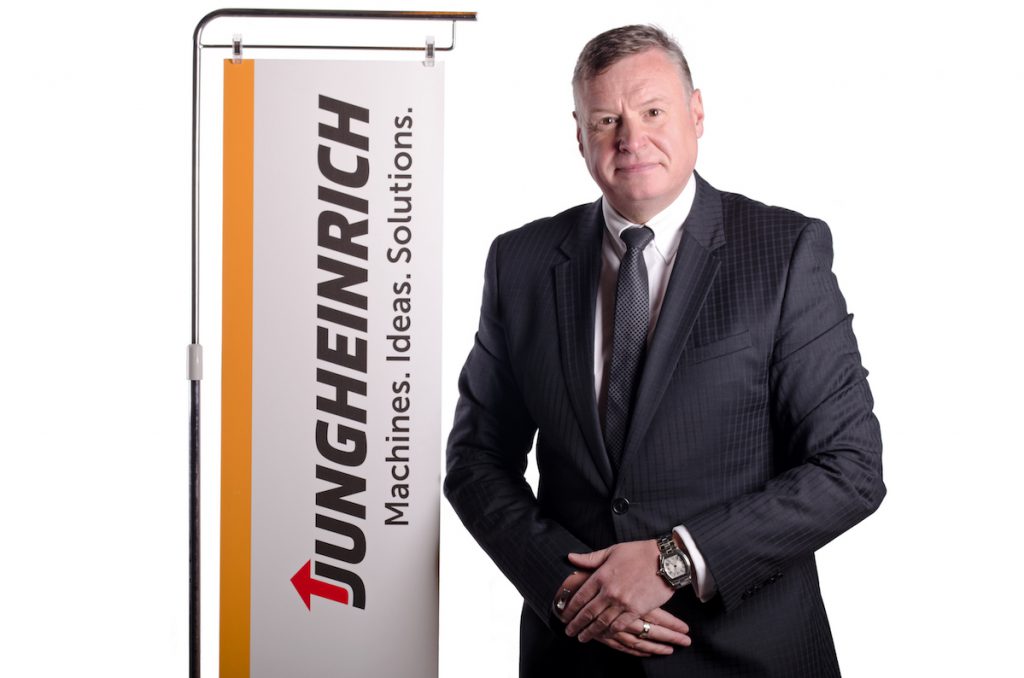
As organisations embrace 24×7 warehousing in response to customer led demands for unprecedented levels of immediacy and visibility, intralogistics operations are increasingly taking centre stage. In a bid to drive productivity, increase efficiency, improve accuracy and reduce costs, automation is now a key consideration for many businesses. Steve Richmond, Director – Logistics Systems, at Jungheinrich UK (pictured), looks at the role of the Warehouse Management System (WMS) in today’s supply chain and why it has to be able to adapt to the evolving needs of a business.
For those planning to implement automation, semi-automation, or indeed optimise their manual processes, one of the most important products to have in place is a robust WMS. Why? Because businesses need to be able to manage existing core logistics processes, along with future proofing business software platforms so that as the company expands, it can respond to change and add automation such as Automated Guided Vehicles, other types of automation or more complex customer-driven picking strategies.
Additionally, recent innovations within the warehouse have seen an increased demand for voice technology and wearable devices. To ensure that businesses are able to introduce the latest technology they must be able to expand the capabilities of their legacy WMS. The initial design and specification of the WMS will determine how flexible a facility will be going forward. For example, if you currently operate a manual warehouse and employ conventional order picking technology, could your WMS adapt if you were suddenly faced with an upsurge of online orders, which brought about a dramatic shift in your typical order profile, such as during peak sales periods?
Order processing profiles and picking requirements may change significantly. For example, a facility may suddenly be required to shift from a bulk or unit load-based operation by a customer-driven need to fulfil single item picks at a much higher frequency. But what if the WMS couldn’t accommodate this change? Within a temperature controlled facility the job of the WMS is, arguably, even more crucial. If, for instance, personnel time within the storage unit is restricted because of the temperature, it is doubly important to make sure workers are as productive as possible. And, with many temperature controlled sites using multi-depth storage systems, it is essential to choose a WMS that has the functionality to recognise and support such methods.
5 Key Points to Consider:
* Recognise where the system’s boundaries are – and ensure that they are flexible enough to move with your demands. If you do not have flexibility in your WMS, your ability to adapt your business model is very limited and your chances of moving with the changing demands of your business will be greatly diminished.
* Select robust software that has an established track record – rather than a system that has been developed uniquely for your use.
* Try to choose a suite that is feature rich – you may not need many of the built-in functions now but it is reassuring to know that they are there and can be switched on in the future should you require them.
* Investigate fully Enterprise Resource Planning systems that boast extensive WMS functionality – in some cases, the WMS can be limited.
* Ensure that your WMS allows for semi- or fully-automated materials handling systems to be introduced in the future.
More and more businesses are optimising their processes and looking at more flexible solutions so that they can remain competitive. What Jungheinrich is seeing is pre-existing WMS systems working hard to ensure that the functions they provide are scalable and able to work with the latest technology. Jungheinrich’s WMS is designed in such a way that it is highly configurable to the needs of each user. In its standard form, the WMS supports an extensive variety of functions as well as centralised master data management. It controls and optimises a range of processes such as incoming and outgoing goods management and order picking.
The software supports the complete transparency of all processes through its extensive reporting features and analysis options. It can be linked to numerous system environments using standard interfaces and can be redesigned to fit with existing systems. The system also offers a series of special functions and extensions for complex logistics processes or automated warehouse facilities. For instance, route management, hazardous substance storage, multi-client capability and material flow modules can be simply added as required.