“Handheld Failures Frustrate Workforce and Cost Business” Says Research
16th January 2020
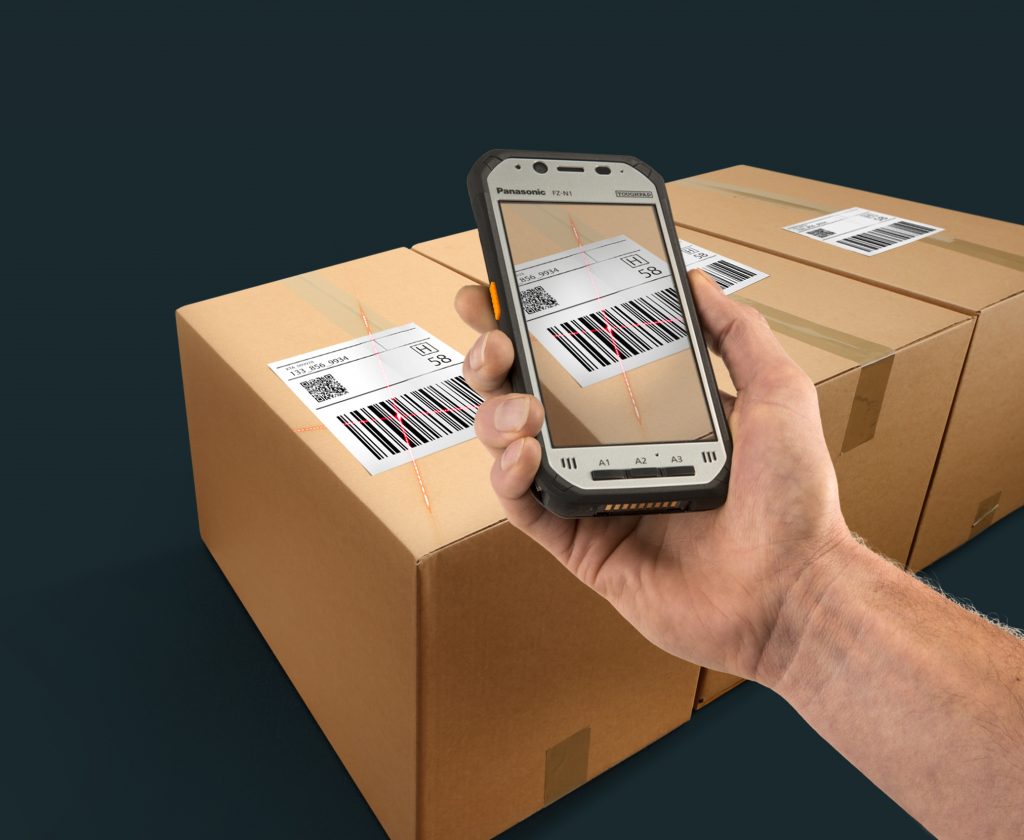
Handheld devices with barcode readers on average fail more than 2.5 times a year and take 2.6 days to repair or replace (1), says latest research carried out on behalf of Toughbook makers, Panasonic.
Handheld mobile computing failures are frustrating delivery drivers, warehouse workers, retailers and emergency services personnel across the UK and costing business, they say.
On average over 63% of workers felt their handheld device was more prone to failure than other technology devices they used. But in this fast-paced business world, device users were certainly not treating their handhelds with kid gloves. Workers reported device damage was caused by a wide variety of issues from drops and spills, to being left in freezing or melting hot conditions to being run over by vehicles!
Problem caused by:
Device dropped 45%
Left it in a hot place 20%
Just stopped working 40%
Dropped in water 12%
Run over by a vehicle 8%
Spilt liquid on device 16%
Left in a cold place 7%
The most frequent damage from these accidents varied from battery, button and touchscreen issues to bar code reader failure.
Top reasons for failures were:
Battery problems 39%
Touchscreen issues 32%
Device stopped working properly 24%
Broken screen 22%
Buttons stopped working 15%
Bar code reader failure 24%
Even when their devices were operating effectively, mobile workers still found them frustrating. The most annoying things about their handheld device were:
Slow or inaccurate bar code 16%
Unable to use wearing gloves 18%
Too heavy 15%
Poor battery life 18%
Poor screen sensitivity for signatures 10%
The top design improvements they would like to see made to their handheld devices were:
Anti-scratch coating 30%
Hand or shoulder strap 28%
Heat reflective coating 18%
Easier to clean 21%
Hot swap batteries 22%
Camera 17%
And if these improvements were made and they had their perfect handheld device, workers promised huge increases in productivity as a result. Workers estimated that they would be 39% more productive on average.
Jan Kaempfer, General Manager of Marketing for Mobile Solutions Business Division – Europe, said: “There can be no doubt that mobile workers are feeling the frustrations of working with their current handheld mobile computing devices. As well as demotivating the workforce, these issues are having a huge cost and customer service impact on the businesses they work for.”
“The pressures are high in the business sectors where these bar code scanning handheld devices are used because every second counts. The work environment is also often difficult and exposed, which has an impact on the number of device accidents and failure rates. As a result, it is more critical than ever that technology buyers understand the device design factors that will have the biggest impact on their workforce and their business – ergonomic design, rugged protection and technology differentiators like hot swappable batteries and daylight visible screens.”
A full copy of the Handheld Troubles research executive summary can be found here.
[1] Based on a sample of 250 UK device users