Egemin supplies integrated transport system with innovative AGVs to Continental
10th April 2015
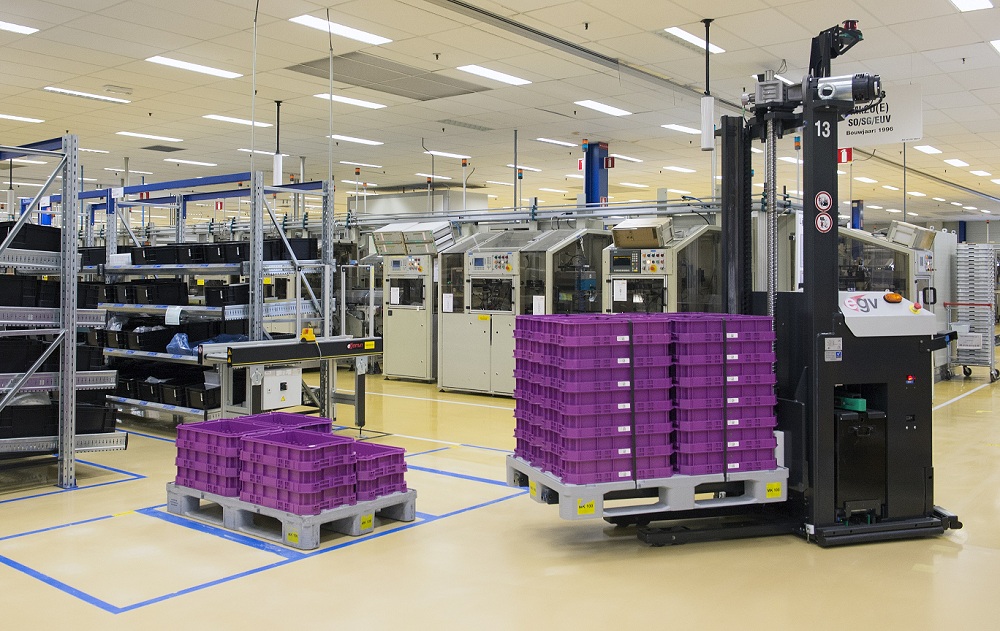
Continental Automotive in Mechelen was recently awarded the first Factory of the Future Award by Agoria. The manufacturer of electronic braking systems (ABS – ESC) won this prize because of, among other things, the extensive innovative automation of its production plant. Egemin Automation supported Continental in this with an innovative transport system with pallet and tote conveyor systems and AGVs (automated guided vehicles). The system handles the transportation of parts and finished goods between the warehouse and production zone and takes over tasks that otherwise need to be done manually.
Thanks to this investment the production environment at Continental is now safer and more efficient. There are no longer any forklift trucks in the production area and quite a lot of manual work is taken over by Egemins Egvs. There is also an increase in efficiency of the processes in terms of timing. The transport conveyors and E’gvs ensure a timely supply of goods to production.
UNIQUE INSTALLATION
Continental brought in Egemin to automate the transport between the automated warehouse and the production zone. Egemin built a turnkey installation with six E’gv®s, a pallet conveyor and tote conveyor system controlled and managed by Egemins E’wcs software (Egemins Warehouse Control System) and E’tricc® software (software for the traffic control and transport management of the E’gv®s) to manage all transport orders.
The components are taken by pallet and a tote conveyor system from the warehouse to the production zone. In the production area, there are four FLV vehicles (Fork Lift Vehicles) for the delivery of pallets with large components and two LTVs (Load Transfer Vehicles) for the delivery of totes with small parts to the production stations. They also return the finished products to the pallet conveyor, which takes them back to the warehouse. Empty totes are returned by the LTVs to the replenishment stations.
What is unique about this installation are the LTVs with six powered roller conveyors that ensure the supply of the flowracks with totes in the correct order. This is possible because the totes are sorted in advance in four sorting lanes on the tote conveyor system according to their destination in the production area. Each sorting lane has one production zone as a destination. The totes are placed in the right order by means of a sequencer depending on the order of the flowracks where the totes have to go. The LTVs then take the totes to the flowracks as instructed by the software. On the other side, the operator takes the tote from the rack and takes out the components.
CHALLENGING PROJECT
The construction of the installation brought with it several challenges. The great diversity of loads (cases, pallets, pallet cages, …) of different sizes and with different fork openings, posed a challenge to the FLVs. In order to solve this, Egemin installed a measuring system at the end of the pallet conveyor that passes the dimensions on to the E’tricc® software. That way, the FLV vehicles can drive dynamically into the pick location, depending on the width of the load and the fork opening.