Hyster enhances ReachStacker for increasing container volumes
5th May 2015
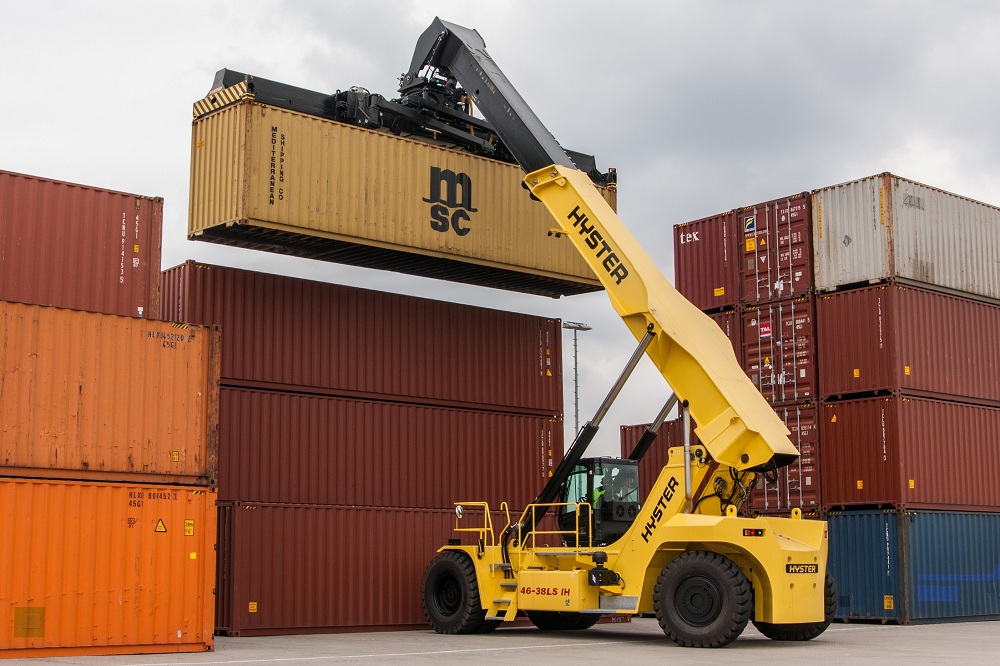
Following a record year for the Hyster® ReachStacker production line, Hyster has made more upgrades to help further reduce lifetime costs, while giving maximum reliability for ports and terminals experiencing increased container throughput.
“The reachstacker market is continuing to grow,” says Jan Willem van den Brand, Product Strategy Manager Big Trucks. “Hyster alone produced more reachstackers than ever last year, for operations all over the world.”
The Hyster ReachStacker is well known for its class leading lift speeds, combined motions of lift and boom extension while driving and exceptional reliability, particularly in 24/7 operations. The incredible performance not only helps terminals move containers quickly, the company claims that it is helping increase the financial margins on container handling.
The busy factory in Nijmegen, the Netherlands, has again recently enhanced the Hyster ReachStacker design to help further reduce operational costs for ports and terminals.
More than 25% fuel savings, which could be more than 4 litres per hour, can be achieved with the new Hyster ReachStacker when compared to our Stage IIIA 2010 trucks and many of our competitor models, confirms Jan Willem. Our goal was to continue our profitable low emissions strategy reducing the total cost of operations and ownership while meeting the new standards for a cleaner environment.
Featuring the new Cummins QSL9 engine and other technologies to meet the Stage IV / Tier 4 final (T4f) emissions legislation, the new Hyster ReachStacker is proven to offer significant fuel savings in real life applications.
Hyster has used heavy EGR (exhaust gas recirculation) combined with SCR (selective catalytic reduction) and a DOC diesel oxidation catalyst to achieve Stage IV / T4f compliance. This has resulted in approximately 96% less particles (soot) and 94% less NOx (nitrogen oxides) compared to Stage IIIA / T3 equivalents before 2005.
EGR reduces NOx formation during combustion, followed by SCR which removes the remaining NOx from the exhaust stream. This combination requires low DEF (Diesel Exhaust Fluid) usage, with no risk of crystallisation. For the PM (particulate matter) reduction, high pressure fuel injection reduces PM formation at source and the diesel oxidation catalyst (DOC) removes the rest from the exhaust stream.
“There is no diesel particulate filter, no additional operator intervention or ash cleaning service required,” says Jan Willem.
In addition to the Cummins engine technologies, Hyster performance optimisation developments such as cooling on demand, ECO-eLo mode, RPM management and alternate engine idle speed, help to further reduce the total fuel consumption. Load sensing hydraulics also allow a high lift speed at low RPM.
The ReachStackers include engine, transmission and hydraulic protection systems, ensuring excellent reliability in the most intense container handling operations.
“Machine availability is critical to a port operation to avoid bottlenecks at busy times,” explains Jan Willem. “The Hyster ReachStacker is a proven design and consistently delivers unbeatable reliability.”
The strong frame and boom design supports 1st, 2nd and third stacking and, depending on the machine, up to 41 tonnes in the 2nd row and 6 high in 1st row. Models are available with container handling or Intermodal handling spreaders, or many different attachments for other industries such as metal or wind power.
The spreader can be rotated by 180 degrees for even more flexibility, allowing containers to be rotated or transported lengthwise. The aisle width remains unchanged at 15 metres (approximately 49′), and with a powered sliding cab, excellent visibility and comfortable driving environment, it is a machine favoured by drivers.
A Central Greasing System has also been introduced to the Hyster® Big Trucks range. There are up to 88 points of a Hyster ReachStacker (subject to the configuration) that are greased and manual greasing can take a long time, so this system helps to ensures that all points are continuously greased, leading to a longer lifetime for the components due to less wear; and reduced maintenance costs and associated downtime.
The manufacturer is also currently working on further improvements to optimise lifetime costs. For example, Hyster is planning to test a remote control system that allows terminal managers in ports to centrally control the container handling machines. This lets the terminal manager change between the economical Eco-eLo mode and HiP mode.
“Another innovation we are testing focuses on tyre wear. When driving without load, if the boom is in a raised position it puts more weight on the tyre, wearing them out unnecessarily quicker. The tyre life enhancement system alerts the driver to correct the boom position,” explains Jan Willem.
The innovative Hyster® Tracker asset management system introduced in 2013 is already bringing significant management benefits to many container handling operations.
“Our larger customers, which include some of the world’s largest shipping lines and logistics firms, choose us because we are a truly global supplier with leading products backed up with global support specialising in Big Trucks.”
All Hyster products are supported worldwide by a network of highly trained dealers providing expert, responsive local service and customisations for specific industries. This includes local availability for specific spare parts required for Big Trucks, including ReachStackers, and engineers located on site where required.
Visit www.hyster.eu.